In this article, we’ll explore the basics of Resistance Temperature Detectors (RTDs). We’ll explain their working principles, applications in industrial temperature measurement, and cover essential aspects such as maintenance, calibration, and troubleshooting of RTD circuits.
How Does a Resistance Temperature Detector (RTD) Work?
At its core, an RTD is a passive resistive device made from metals, typically platinum, that change resistance as the temperature changes. Simply put, when the temperature increases, the resistance of the RTD also increases. For example, a Pt100 RTD, made from platinum, has a nominal resistance of 100 ohms at 0°C. This characteristic makes RTDs reliable and precise in measuring temperatures.
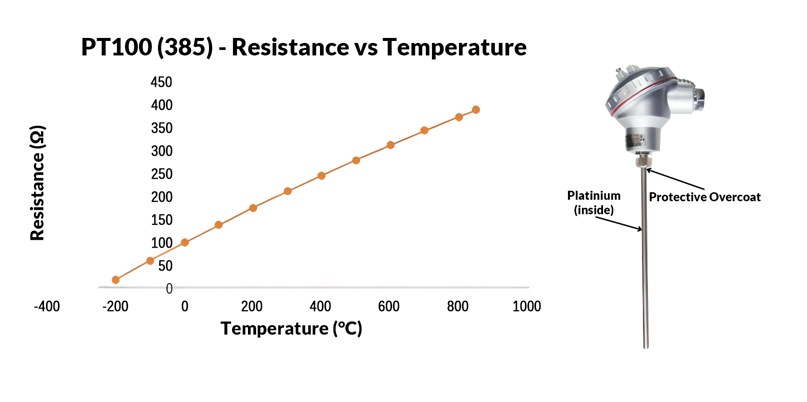
Industrial Applications using PT100
In industrial settings, Resistance Temperature Detectors are typically powered by a small electrical current to measure temperature precisely. Other temperature measurement devices like thermocouples and thermistors are also used, but Resistance Temperature Detectors have an advantage due to their linear resistance change with temperature..
For instance, a Pt100 RTD has a linear range from 0°C to 400°C, and its temperature-resistance relationship is defined by a constant called the temperature coefficient (or Alpha), which for a Pt100 is 0.00385 ohms per ohm per °C. This can be simplified to a resistance change of about 0.385 ohms per degree Celsius.
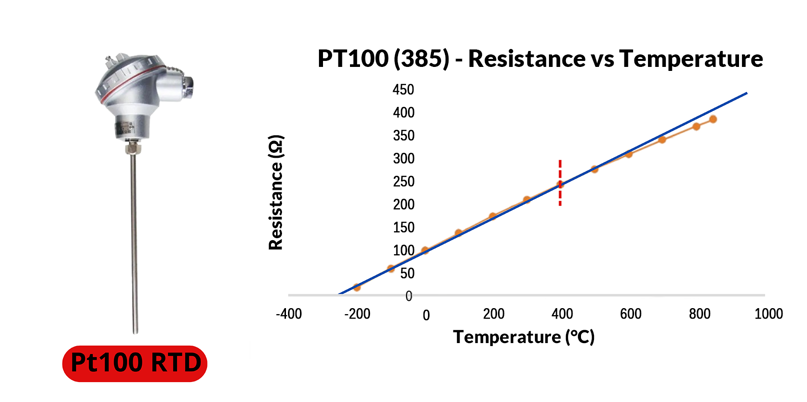
Methods of RTD Resistance Detection
In the past, one common way to detect RTD resistance was through a Wheatstone Bridge, which allowed for voltage measurements proportional to the RTD’s resistance. However, the Wheatstone Bridge has some limitations, such as interference from lead wire resistance and supply voltage drifts, so it’s not as widely used today.
More modern methods involve constant current sources, which are less affected by these issues. With a constant current source, the resulting voltage across the RTD gives a direct indication of temperature without being skewed by external factors.
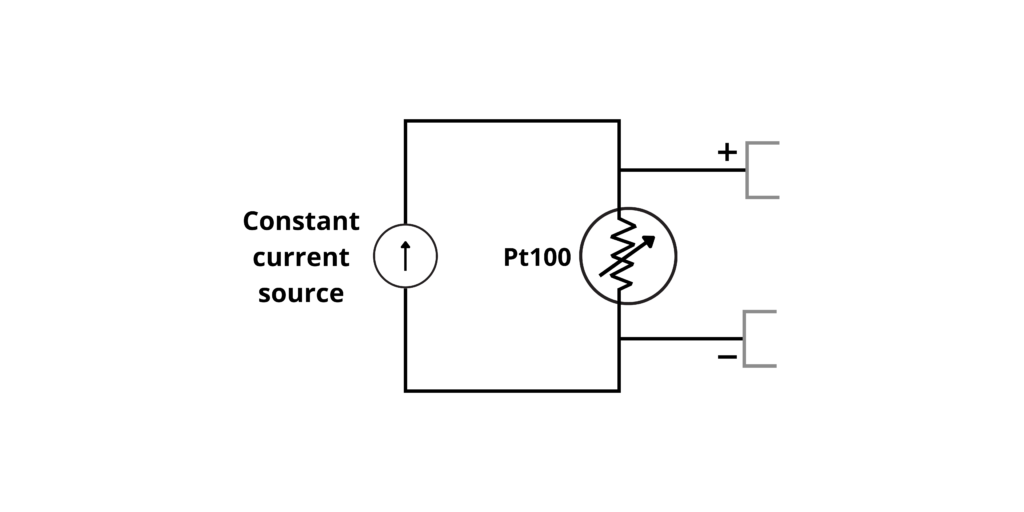
RTD Configurations: 2, 3, and 4-Wire measurement
RTDs come in several configurations. The basic 2-wire RTD is prone to inaccuracies due to lead wire resistance, so it’s rarely used in industrial applications. The 3-wire and 4-wire configurations are much more common. A 3-wire RTD connected to a Wheatstone Bridge can compensate for lead wire resistance, while a 4-wire RTD with a constant current source is often considered the most accurate setup, especially in environments where precision is critical.
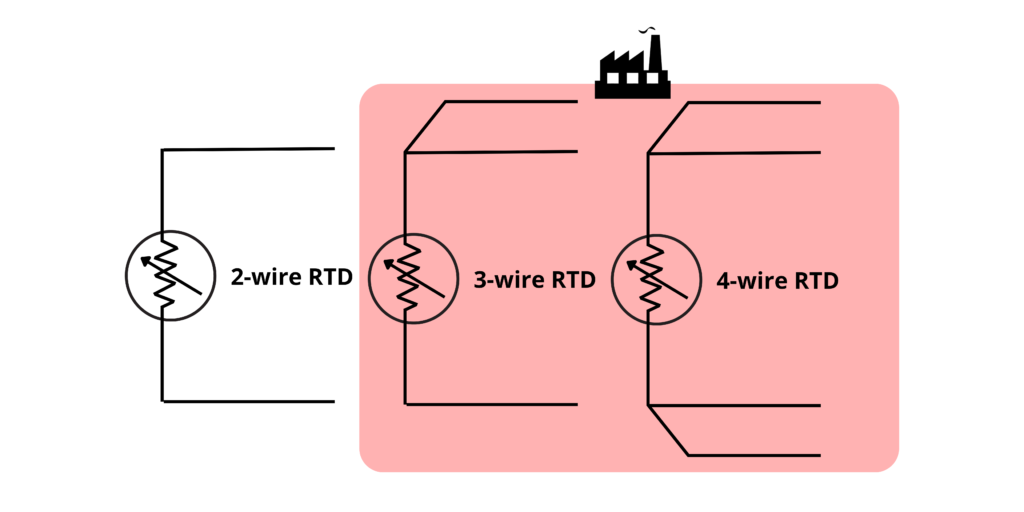
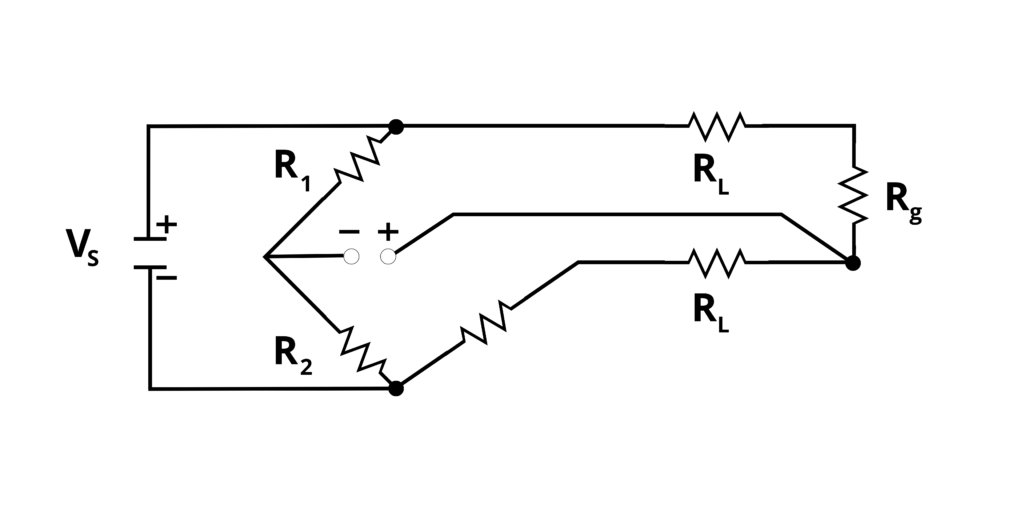
How to process RTD signals for the S7-1200 PLC
To process RTD signals with a Siemens S7-1200 PLC, connect the RTD sensor (e.g., PT100) to an analog input module designed for RTD signals, such as the AI 4xRTD ST module. In TIA Portal, configure the module by selecting the RTD type, temperature range, and filtering options. The PLC will convert the RTD’s resistance to temperature data, which can be scaled and used in the control program. A typical connection involves wiring the RTD directly to the module’s input terminals according to the module’s wiring diagram.
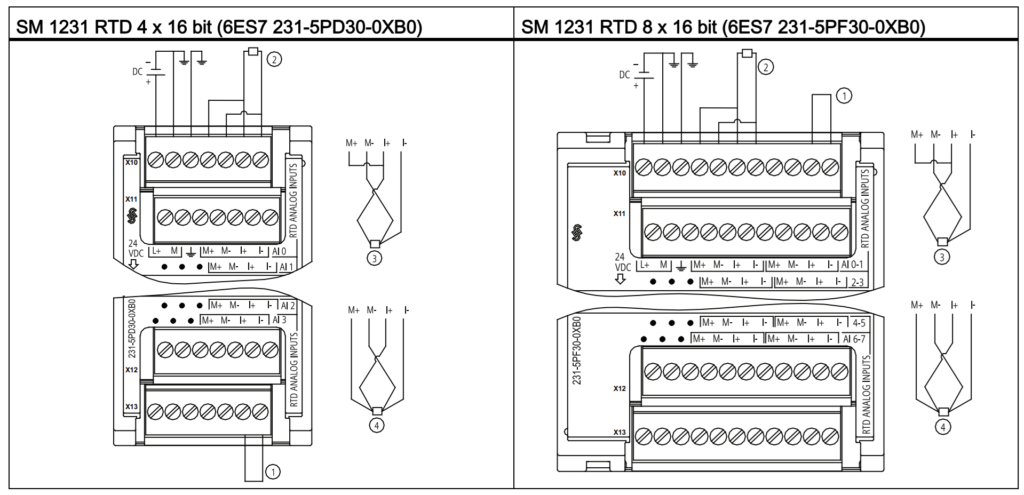
System Manual”
Protecting RTDs and Troubleshooting
Since Resistance Temperature Detectors are sensitive, they need protection from harsh environmental conditions. This is done by housing the RTD in a thermowell—a protective sleeve that ensures Resistance Temperature Detectors maintain accuracy without being exposed directly to extreme conditions
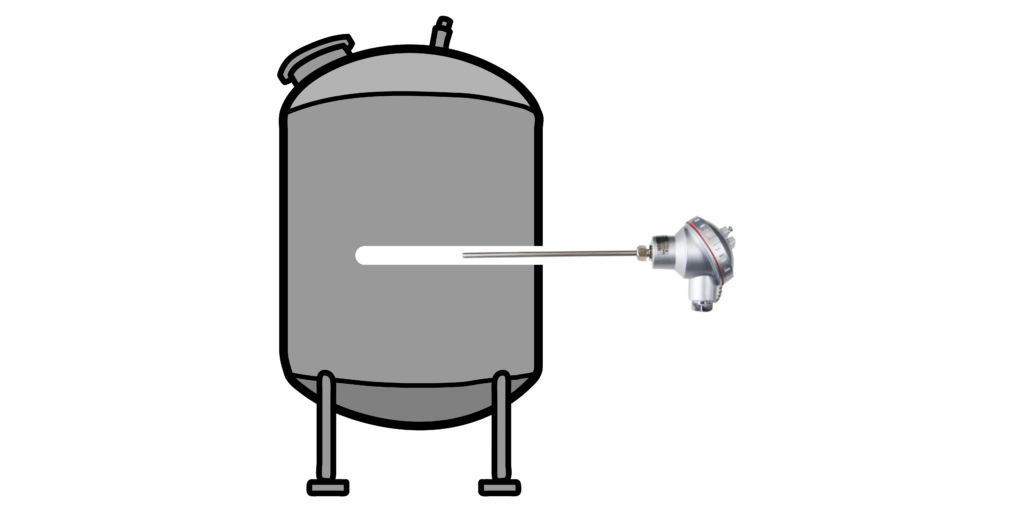
When it comes to maintenance and troubleshooting, common issues include corrosion, moisture, or poor connections, all of which can cause erratic temperature readings. To check if an RTD is working properly, you can use an ohmmeter to measure its resistance. If the readings are off, the RTD might be faulty, and further diagnostics can be done with a process calibrator. This tool simulates the RTD in the measurement circuit to determine whether the problem lies with the RTD or elsewhere in the system.
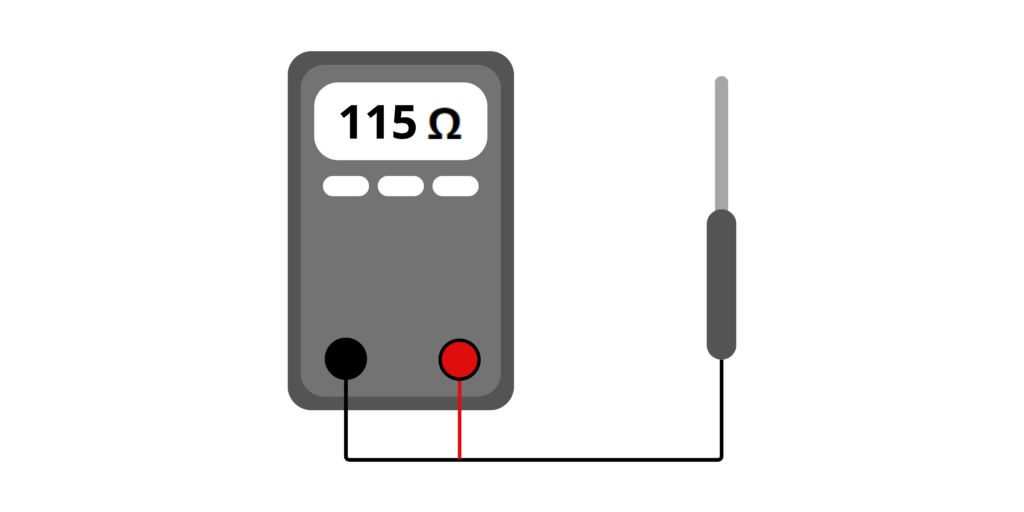
Summary
To recap:
- An RTD is a resistive device that changes resistance as temperature changes.
- RTDs are known for their almost linear resistance-temperature relationship.
- Wheatstone Bridges were once commonly used for RTD detection but have been replaced by more accurate constant current methods.
- RTDs typically come in 3-wire or 4-wire configurations, with the 4-wire being the most precise for industrial use.
- RTDs are protected by thermowells and require regular maintenance and troubleshooting to ensure accurate temperature readings.
- Understanding RTDs can give you a solid foundation in temperature measurement, especially if you’re looking to apply this knowledge in an industrial context.