In industrial automation, control systems play a foundational role in maintaining smooth and efficient operations. These systems are typically divided into two main categories: discrete control and process control.
Types of Automation Systems in Industrial Control: Discrete and Process Control
Discrete Control Systems
Discrete control systems manage specific, individual events, often handling on-off or start-stop operations for machinery. Common applications include conveyor belt systems that queue items for subsequent processing stages in manufacturing. Another example is in automotive assembly, where robotic arms are programmed to weld car parts sequentially, ensuring high accuracy and efficiency.
Sensors in discrete systems often include photo-eye and proximity detectors, along with actuators like drives and mechanical setups such as conveyor belts and robotic units
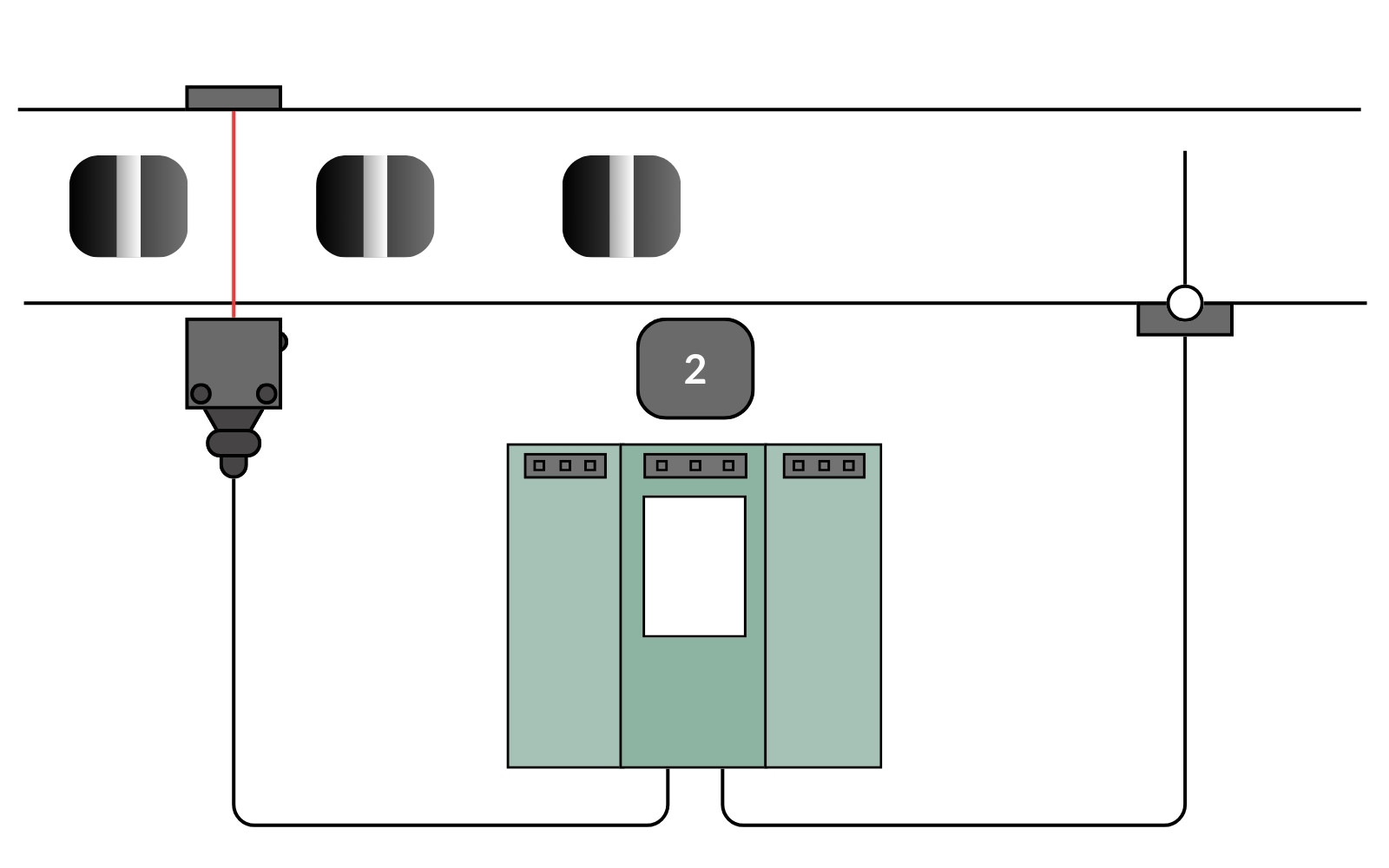
Process Control Systems
Process management systems focus on the continuous monitoring and adjustment of various process variables to maintain desired outcomes. This approach is essential in industries where stable conditions—such as temperature and flow rate in oil refining or consistent mixing and heating in food production—are crucial for product quality.
These systems rely on sensors to measure variables like pressure, temperature, flow, and level. They also use actuators, such as regulating valves and variable frequency drives, to make necessary adjustments. Operating continuously, these systems are pivotal in ensuring reliable and consistent results in automated processes.
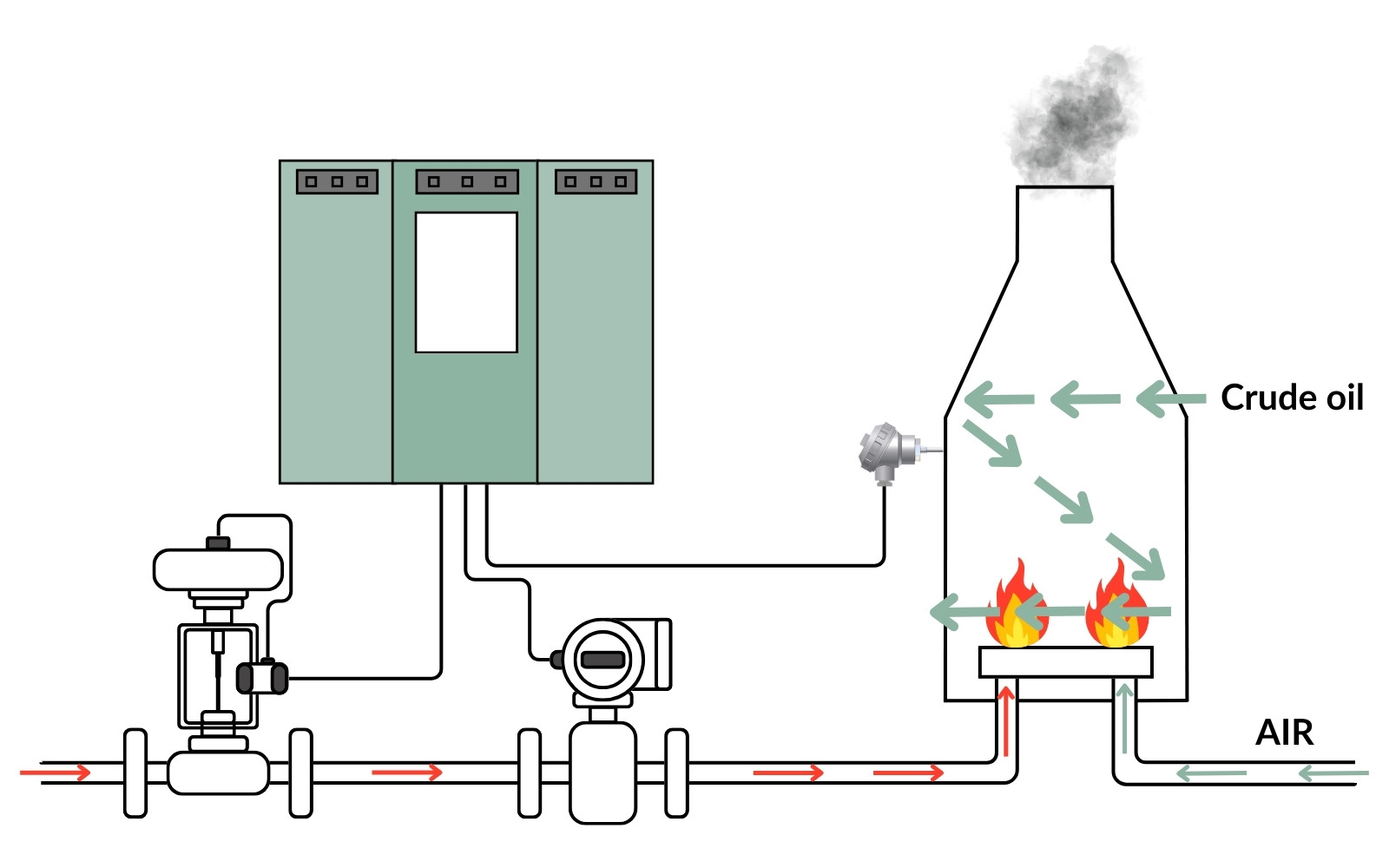
Key Advantages of Industrial Automation: Stability, Efficiency, and Safety in Process Control
Process control is fundamental to stability, consistency, efficiency, and safety in industrial operations, especially in sectors like manufacturing, oil and gas, and pharmaceuticals. Unlike a human operator, who can typically monitor only a few parameters simultaneously, control systems can track thousands of sensors and actuators, enabling real-time adjustments to maintain operational consistency.
Process control aims to achieve four primary objectives: maintaining stability in process conditions, ensuring consistent product quality, optimizing resources to improve efficiency, and safeguarding personnel and the environment.
Essential Components in Process Control: The Role of Programmable Logic Controllers (PLCs)
Programmable Logic Controllers (PLCs) are essential for achieving systems control goals. As specialized computers, PLCs automate and monitor industrial systems, providing the precision and reliability needed. There are many PLC models, each with unique features, produced by over 25 major manufacturers globally.
Key Criteria for Selecting a PLC: Performance, Scalability, and Cost Efficiency
Several factors should be taken into account when selecting a PLC for process control:
- Performance: The PLC should have the speed, reliability, and processing power necessary for the specific application.
- Ease of Programming: User-friendly software and standard programming languages like ladder logic and function blocks make programming and troubleshooting more accessible.
- Scalability: The PLC should allow for future expansion with options for memory, remote I/O, and flexible input/output card support.
- Integration: Smooth integration with other plant systems, such as Human-Machine Interface (HMI) stations, and compatibility with communication protocols like Industrial Ethernet is essential.
- Cost: Beyond the initial purchase, ongoing maintenance costs and the overall cost of ownership should also be evaluated.
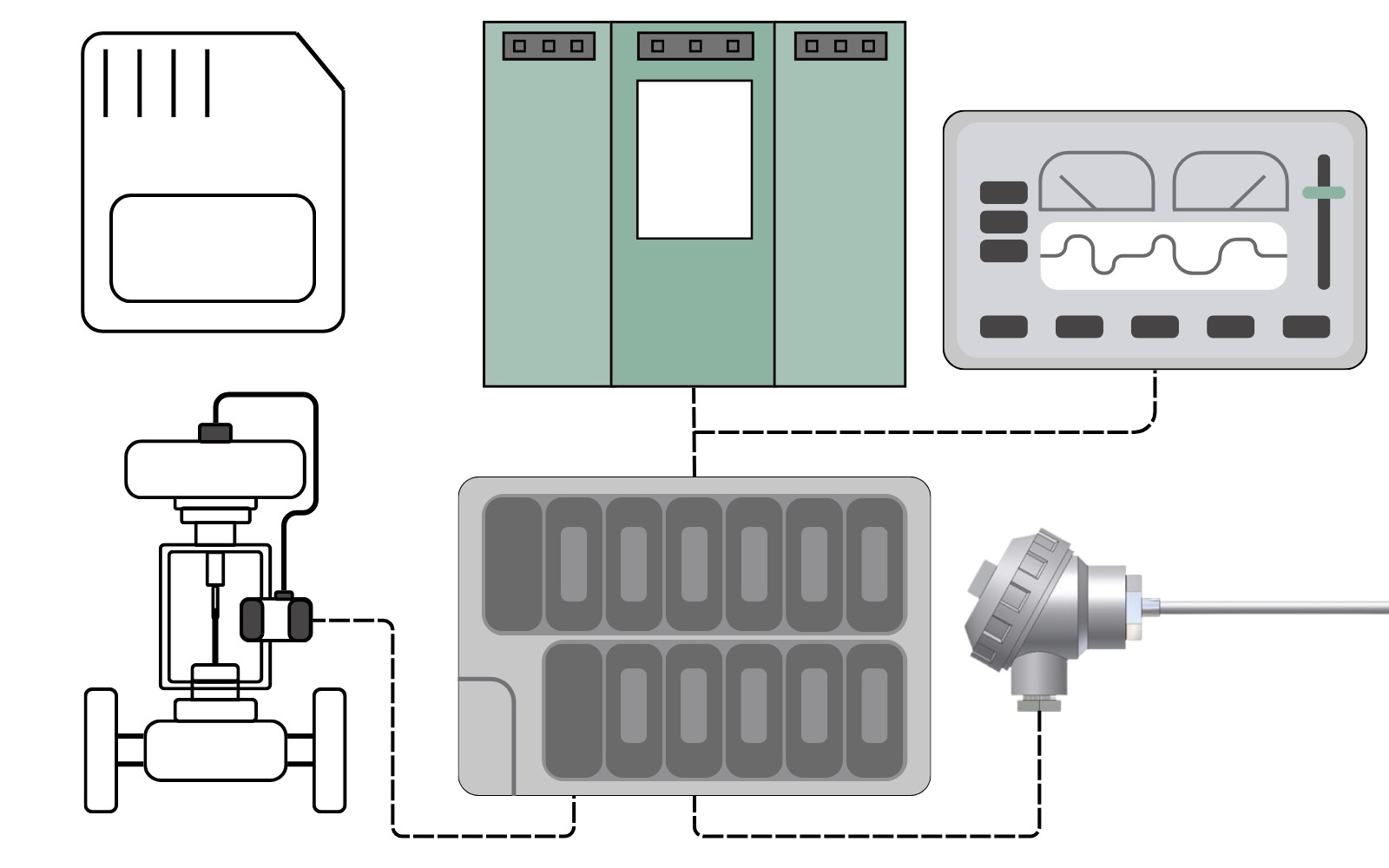
Top PLC Models Across Different Types of Industrial Automation
Siemens SIMATIC S7
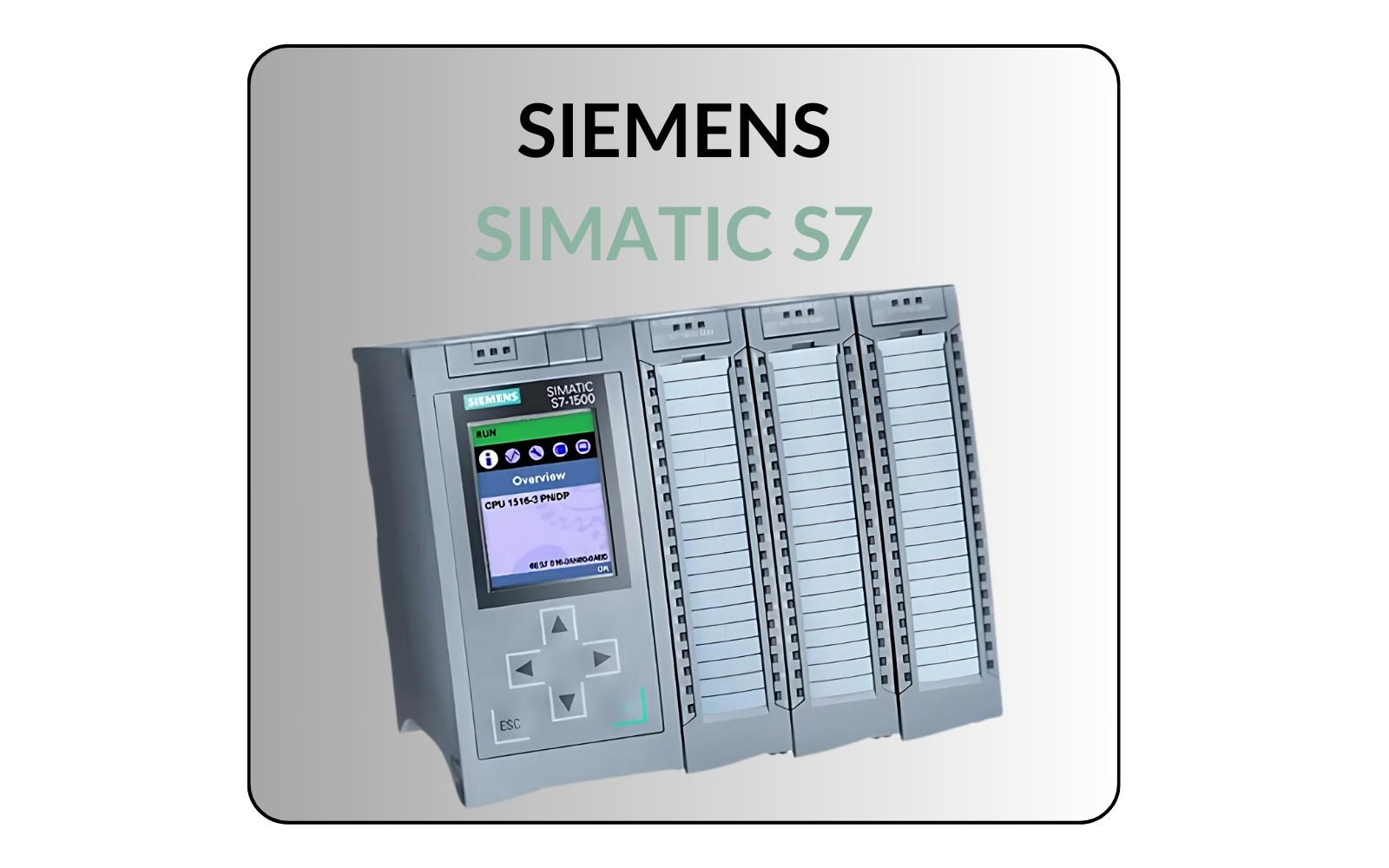
For over three decades, Siemens’ SIMATIC S7 has been an industry standard, recognized for its reliability and robust performance. Its modular design and extensive compatibility with various systems via industrial ethernet protocols, including OPC-UA, make it a popular choice. However, its higher cost and moderate setup complexity can be limiting factors.
Allen-Bradley ControlLogix
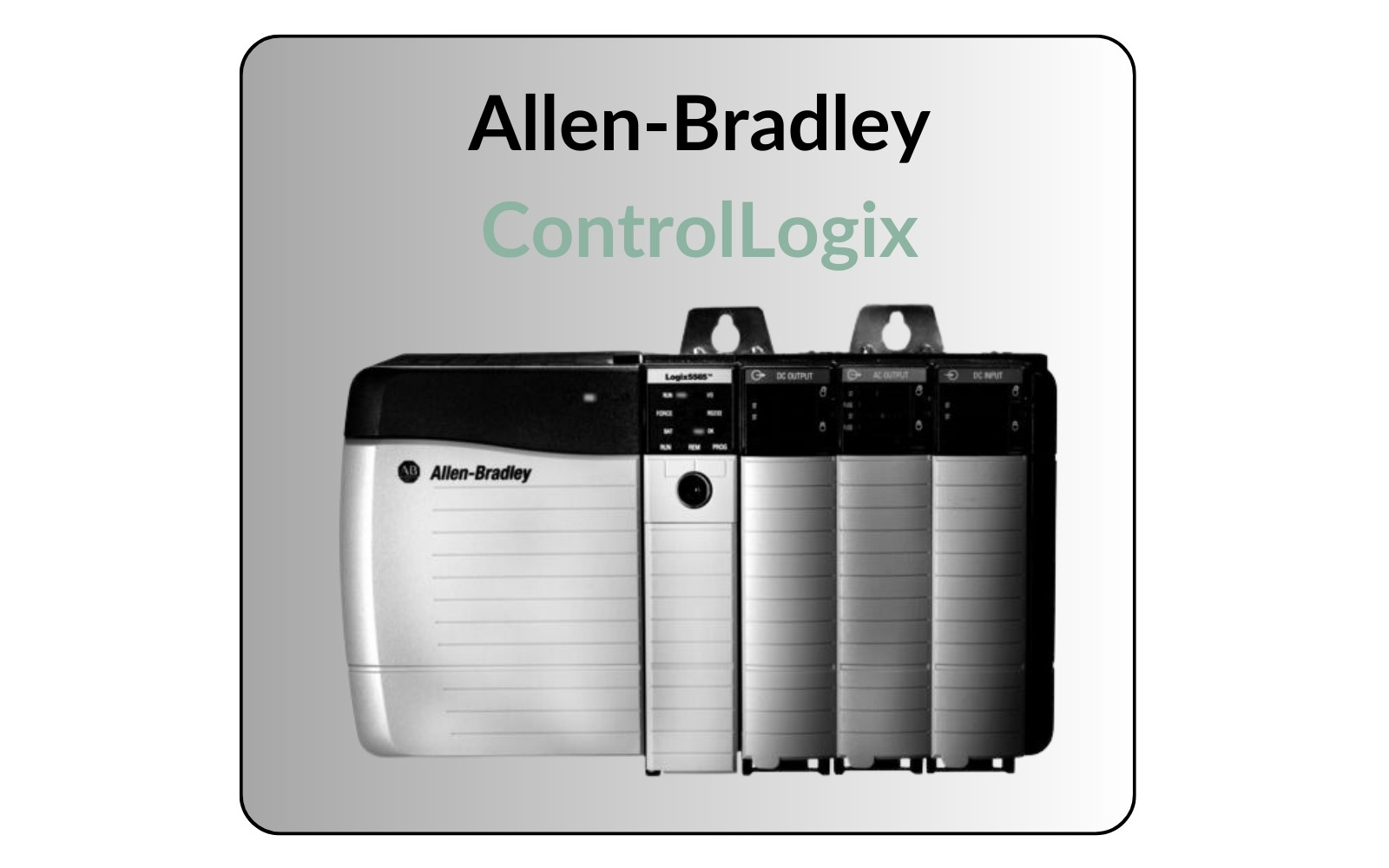
Allen-Bradley’s ControlLogix series offers user-friendly programming and solid performance. Known for its ease of programming and reliability, ControlLogix systems provide extensive I/O interface options. The higher processor cost and potential challenges with processor messaging may present considerations for some applications.
Mitsubishi MELSEC
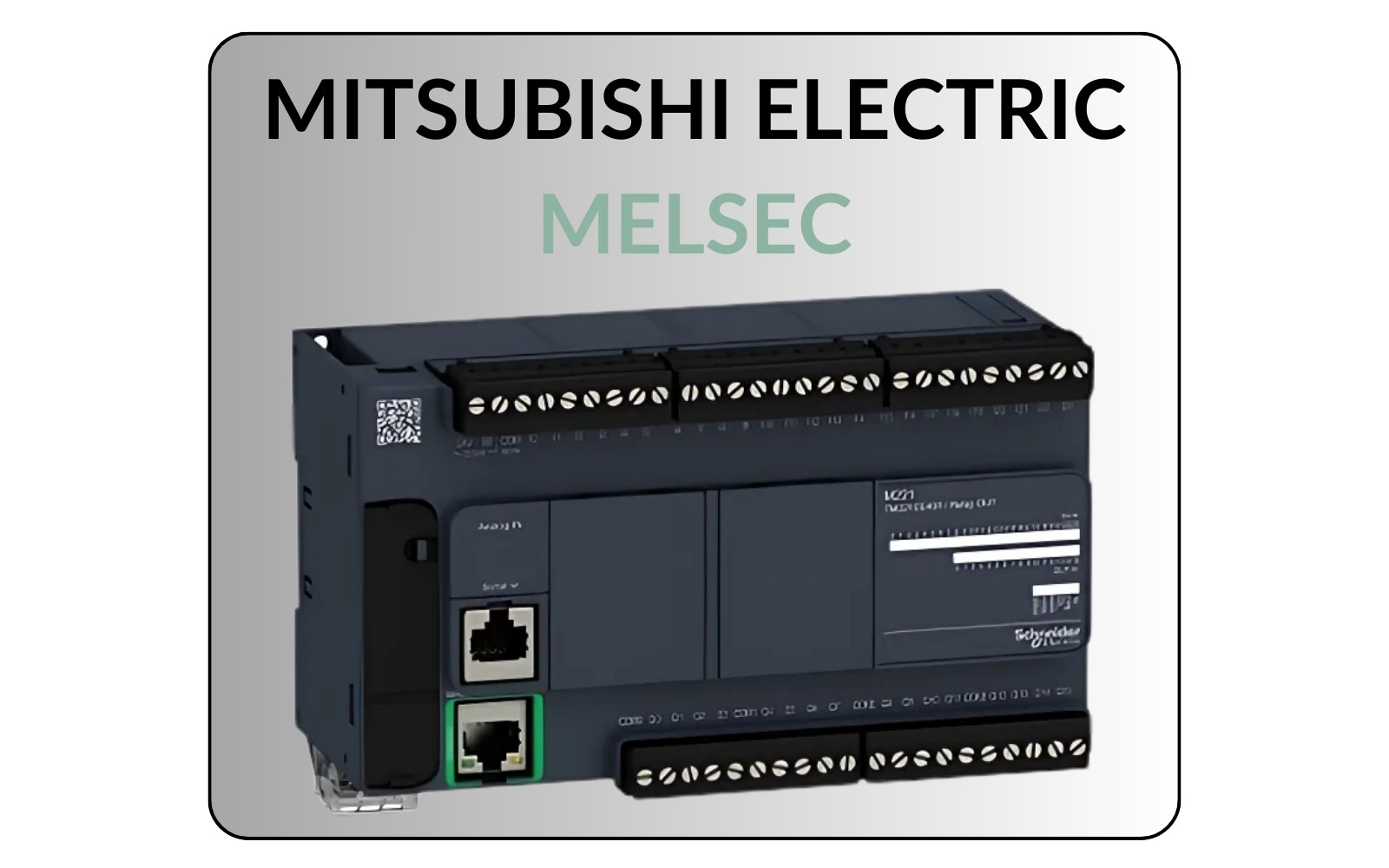
Mitsubishi’s MELSEC series is a cost-effective option, especially suitable for small to mid-sized applications. It is affordable and reliable, though its scalability is more limited compared to higher-end PLCs. Additionally, integrating non-Mitsubishi communication protocols may be complex.
Schneider Electric Modicon
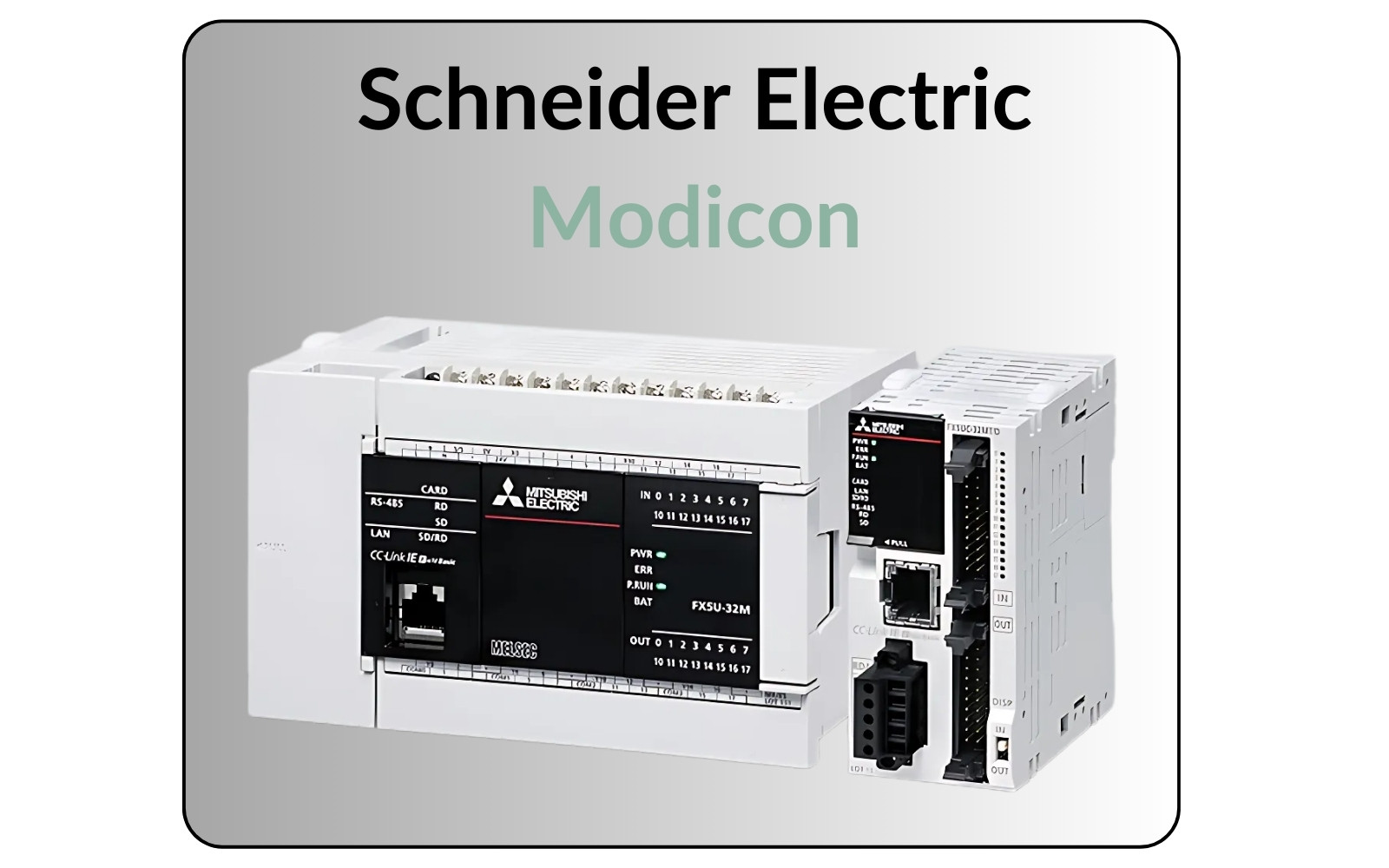
Schneider Electric’s Modicon PLCs are versatile and well-suited for integration with other systems. While they offer scalability, Modicon systems may not deliver the same high performance as other top-tier options for demanding applications.
The Role of Process Control in Industrial Automation
Case Study 1: Hydraulic Press with Siemens S7-1200 PLC
In an industrial setting using a hydraulic press, Siemens S7-1200 PLCs serve as effective automation solutions by monitoring and managing press operations, handling multiple I/O points to ensure precision and safety. The modular design of the S7-1200 supports detailed regulation of pressing cycles, precisely adjusting pressure and timing. This setup helps maintain product quality by keeping each press within optimal parameters and reduces the risk of malfunctions, thereby enhancing overall safety during operation.
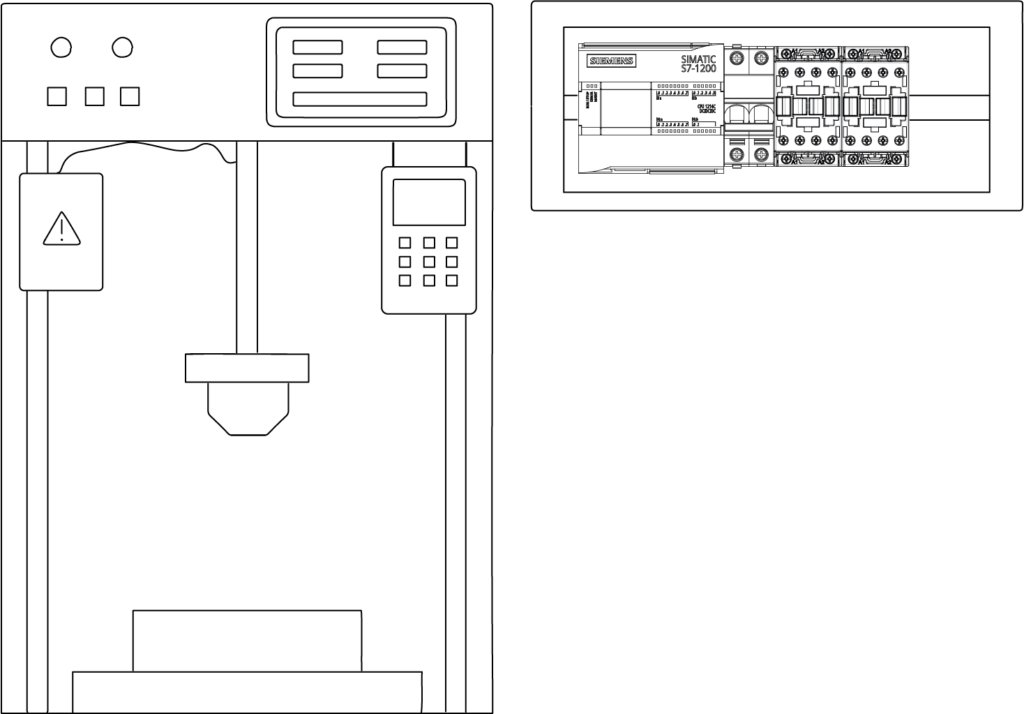
Case Study 2: Manufacturing Plant Using Allen-Bradley ControlLogix
In a water treatment facility, Allen-Bradley ControlLogix PLCs are implemented to automate filtration and chemical dosing processes, ensuring consistent water quality and regulatory compliance. ControlLogix’s precision control capabilities manage pump speeds, valve positions, and chemical injection rates across the facility, optimizing water flow and treatment efficiency. The intuitive programming interface allows operators to make rapid adjustments as needed, minimizing downtime and maintaining smooth, uninterrupted operations.
Case Study 3: HVAC System in Commercial Building Using Mitsubishi MELSEC
A large commercial building utilizes Mitsubishi MELSEC PLCs to control its HVAC (heating, ventilation, and air conditioning) systems, ensuring energy-efficient temperature management across multiple floors. The MELSEC PLCs monitor temperature, humidity, and airflow, adjusting the HVAC equipment in real time to maintain optimal conditions. By coordinating various compact MELSEC controllers, the building achieves precise climate control, reducing energy consumption and operational costs while enhancing occupant comfort.
Conclusion: Key Takeaways for Automation in Manufacturing and Industrial Sectors
Both separate and procedure control systems are essential to industrial automation. Selecting a PLC involves weighing factors like performance, ease of programming, scalability, integration, and cost. Models such as Siemens SIMATIC S7, Allen-Bradley ControlLogix, Mitsubishi MELSEC, and Schneider Electric Modicon each offer unique strengths.
Ultimately, the choice depends on specific requirements and application needs. For those seeking further insight into PLC programming, specialized training resources are available to build foundational skills for various control systems.
Thank you for reading! If you’re interested in learning more, explore our courses for in-depth training: Control Byte Courses.