How to Reduce Inrush Current in Three-Phase Motors with Star Delta Starter
Here’s the main concept: When a three-phase motor is started, it initially pulls up to eight times its rated current. This significant inrush of current can potentially harm the motor windings and negatively impact the electrical network. With a star-delta starter, you can reduce inrush current!

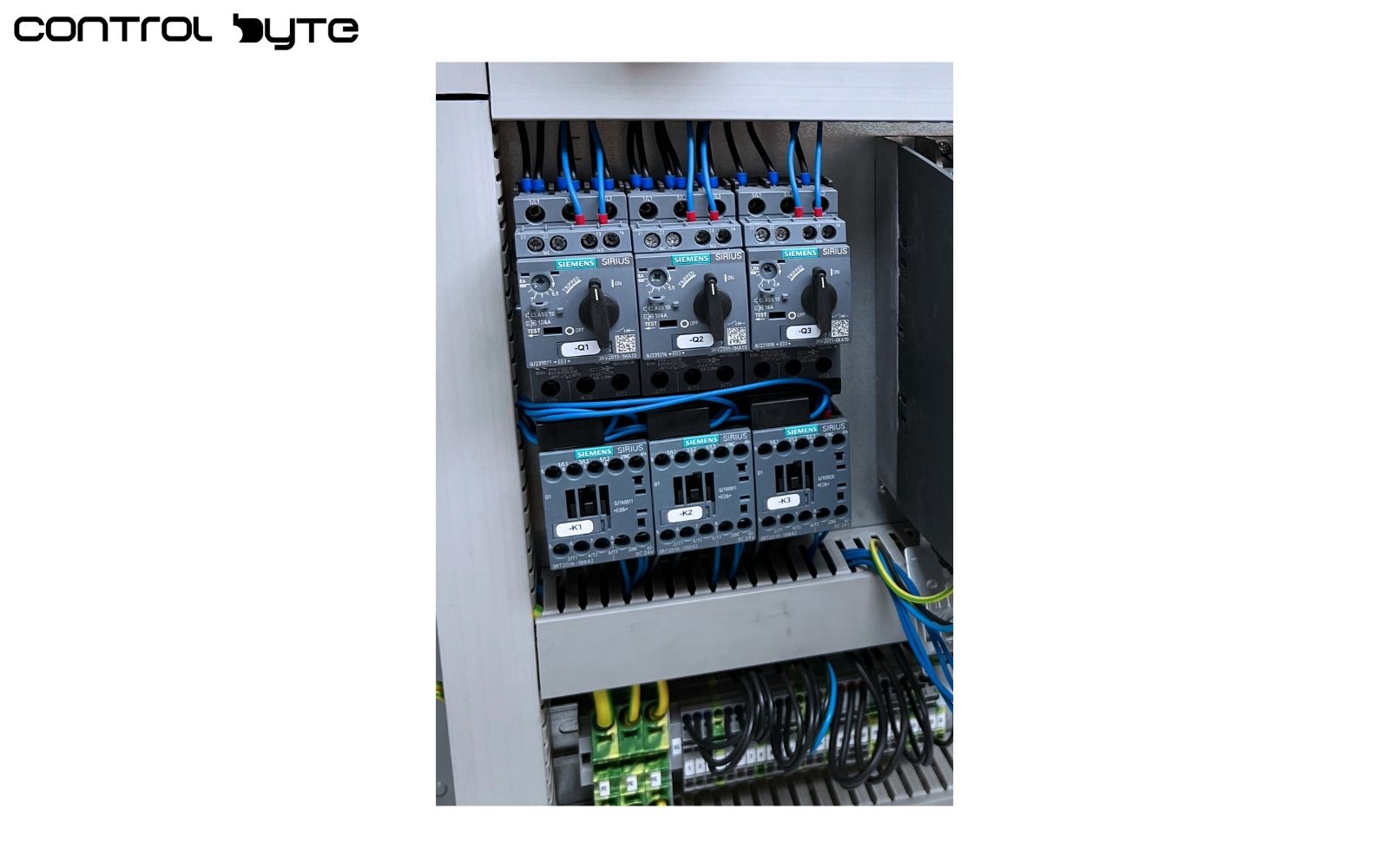
Connecting a Three-Phase Motor to a PLC
With a star-delta starter, the motor begins operation in a star connection, and after a short period, once it reaches adequate speed, the connection is switched to a delta. Operating in star connection initially reduces the startup current since the motor, in this configuration, draws only one-third of its rated current. This approach helps mitigate the excessive current during star tup.
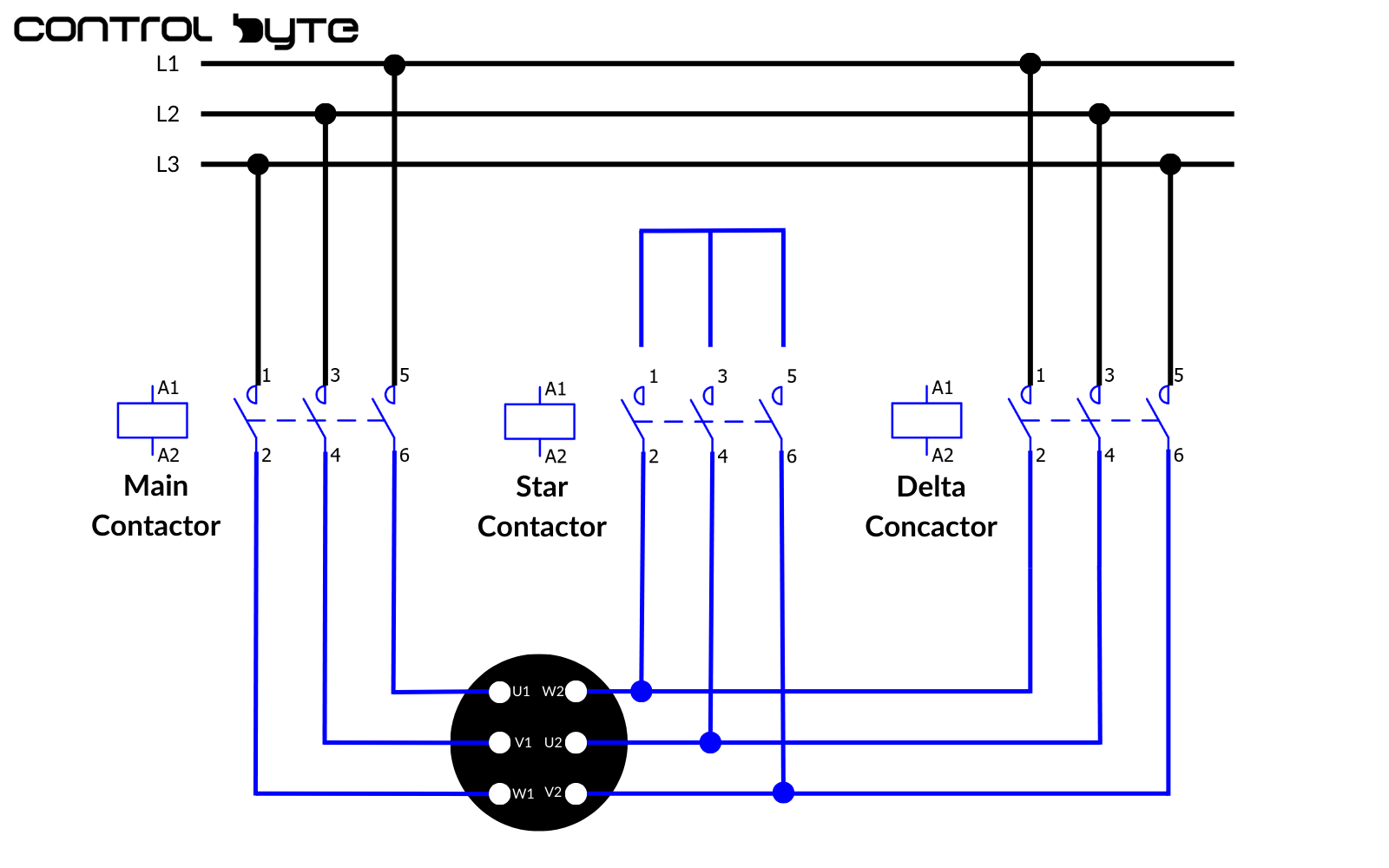
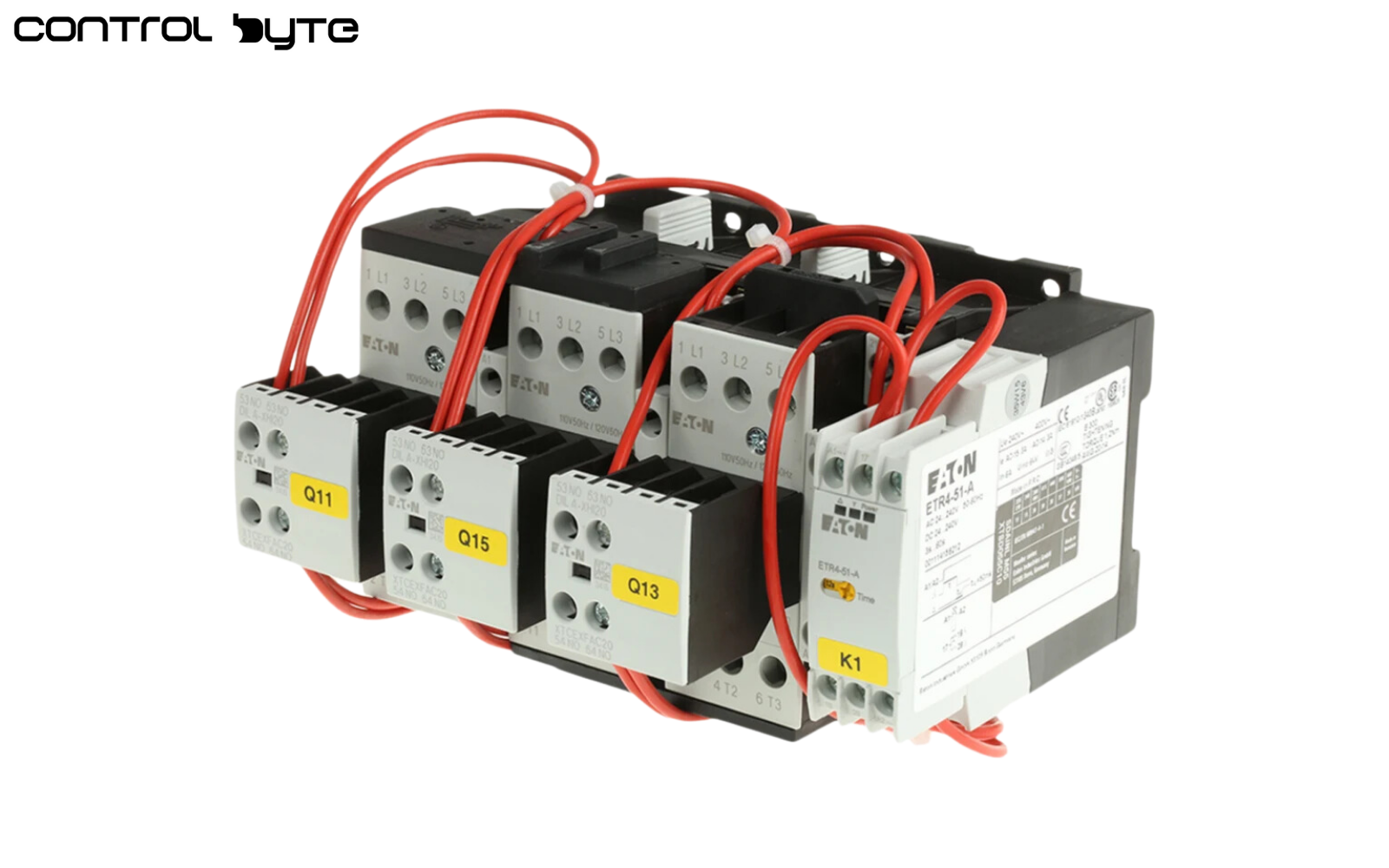
How Basic Switches and Contactors Work in Motor Control
Imagine you have a lamp you want to turn on. To do this, it needs to be connected to a power source. Once connected, the lamp will stay illuminated continuously..
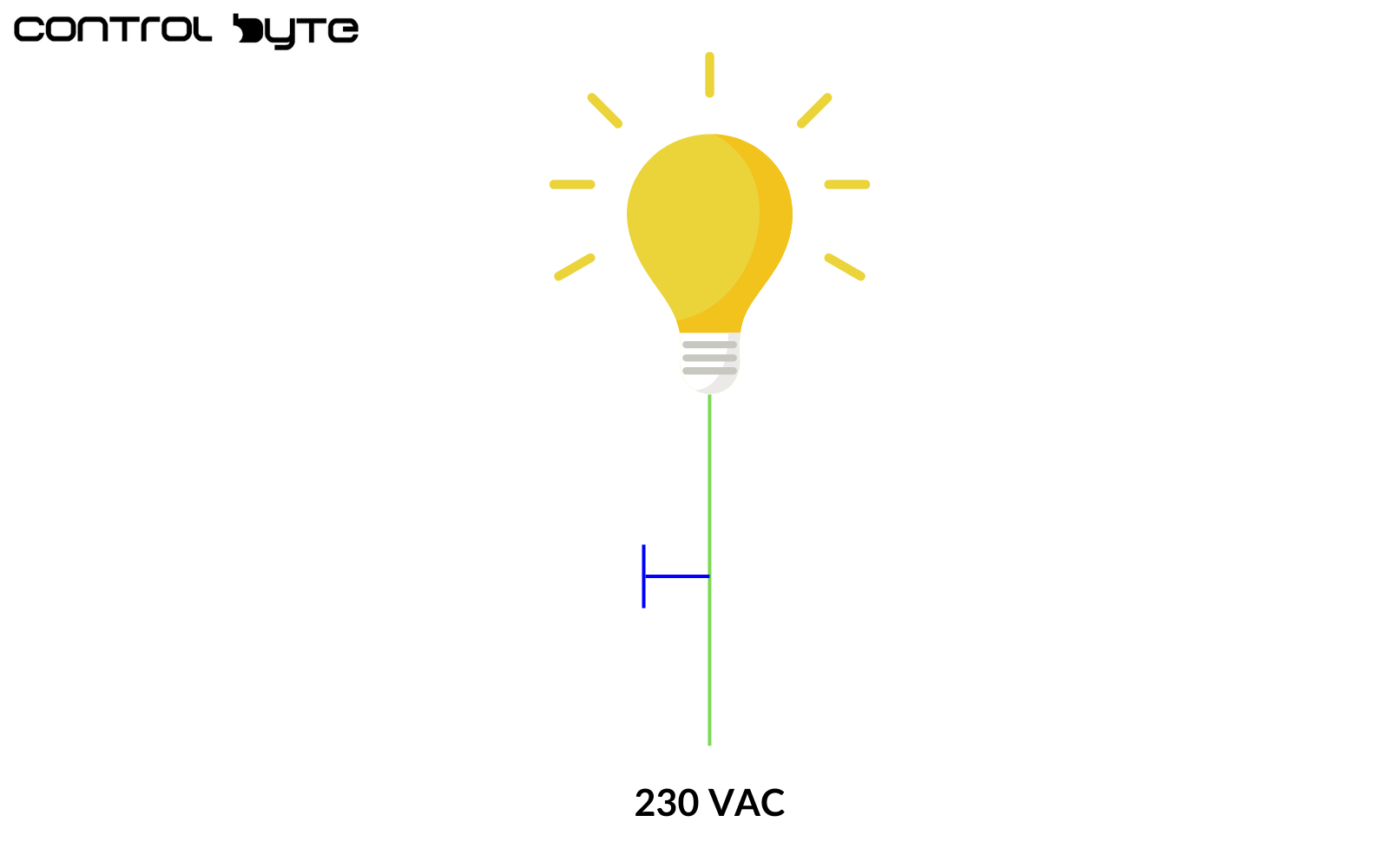
If you’d like to control when the lamp turns on and off, you can add a simple switch. This switch allows you to operate the lamp whenever you need.
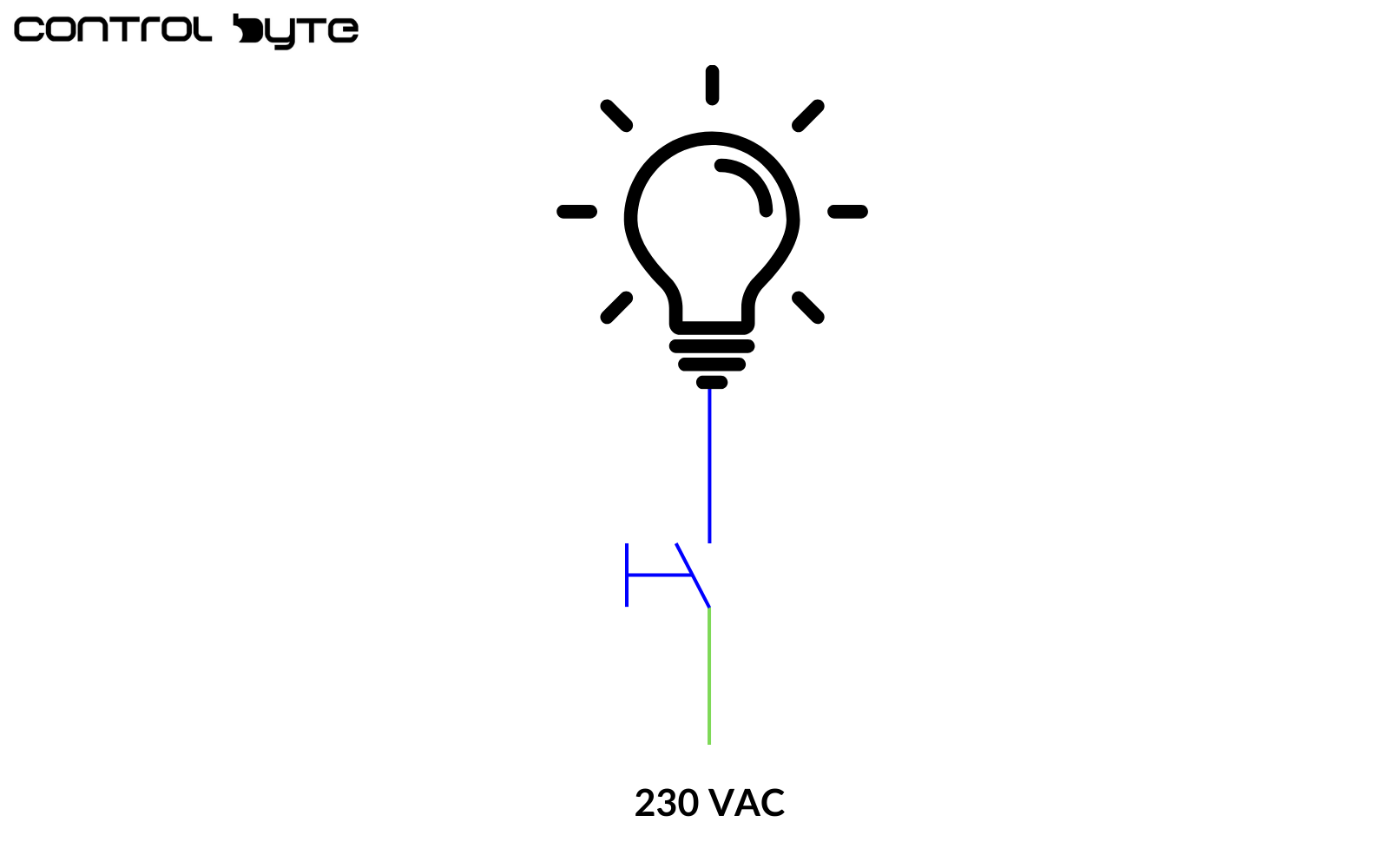
Now, let’s imagine replacing the lamp with an electric motor. To power it on, you’ll need to connect it to a three-phase power circuit.
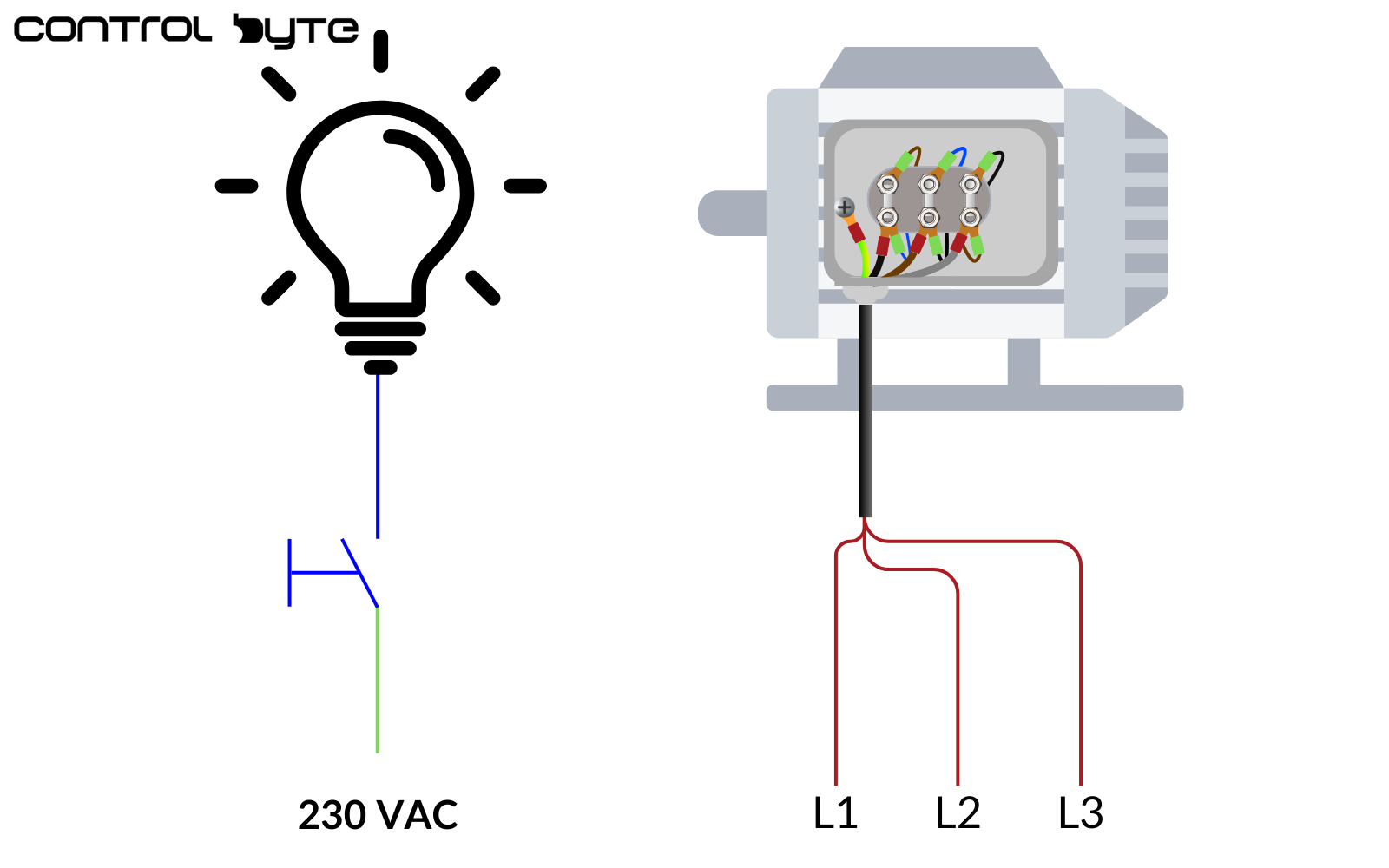
Just as with the lamp, you might want the ability to turn the motor on and off as needed. Here, however, there’s a slight difference: instead of a regular switch, an industrial switch is required, known as a “contactor.”
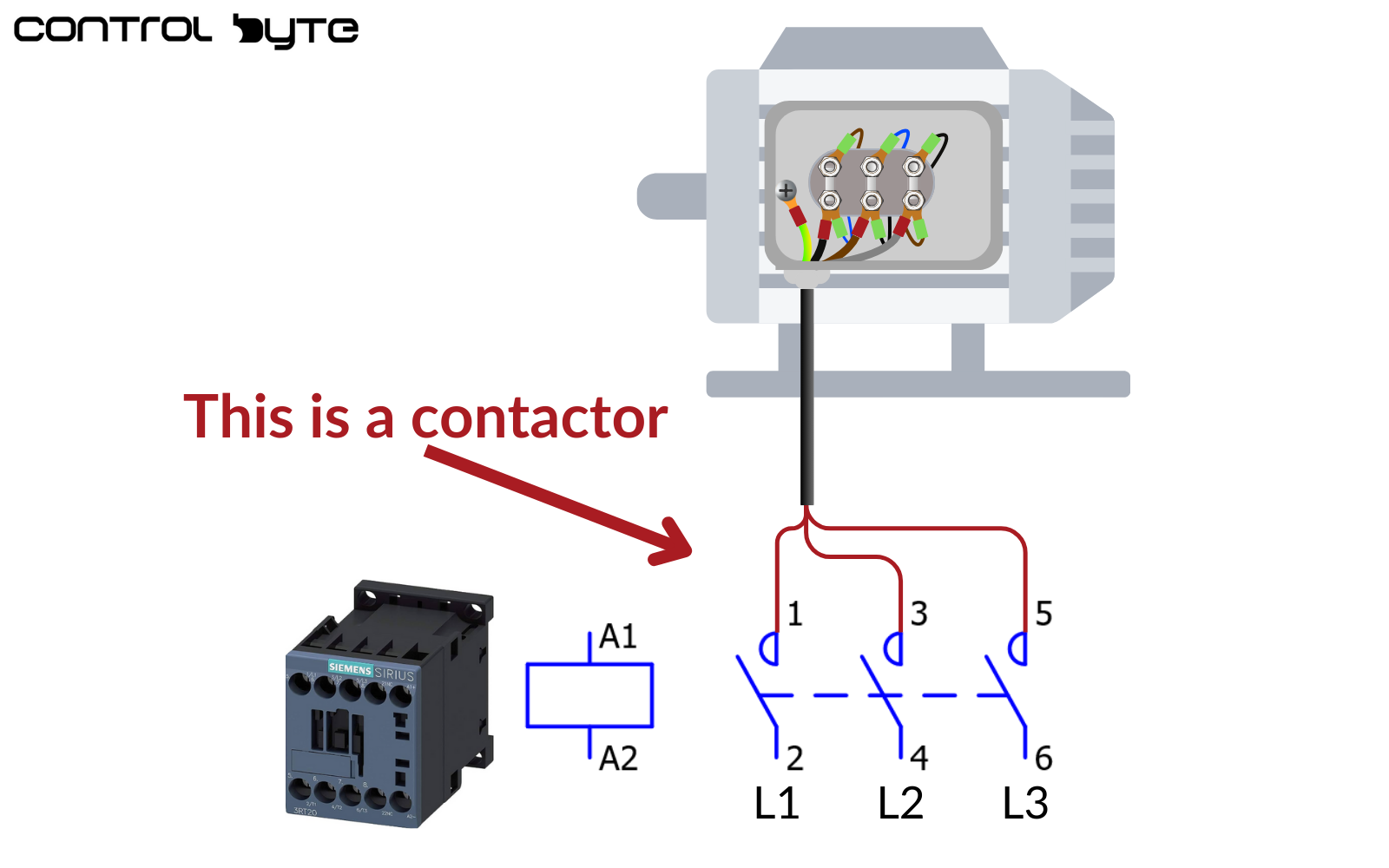
Understanding the Role of Contactors in Motor Control Systems
A contactor consists of two main parts: a coil (electromagnet) and contacts. When power is applied to the coil, it energizes, creating an electromagnetic field. This field closes the contacts, allowing current to flow from the source to the load.
The contactor operates with a simple principle: when the coil is energized, the electromagnetic field it generates closes the contacts.
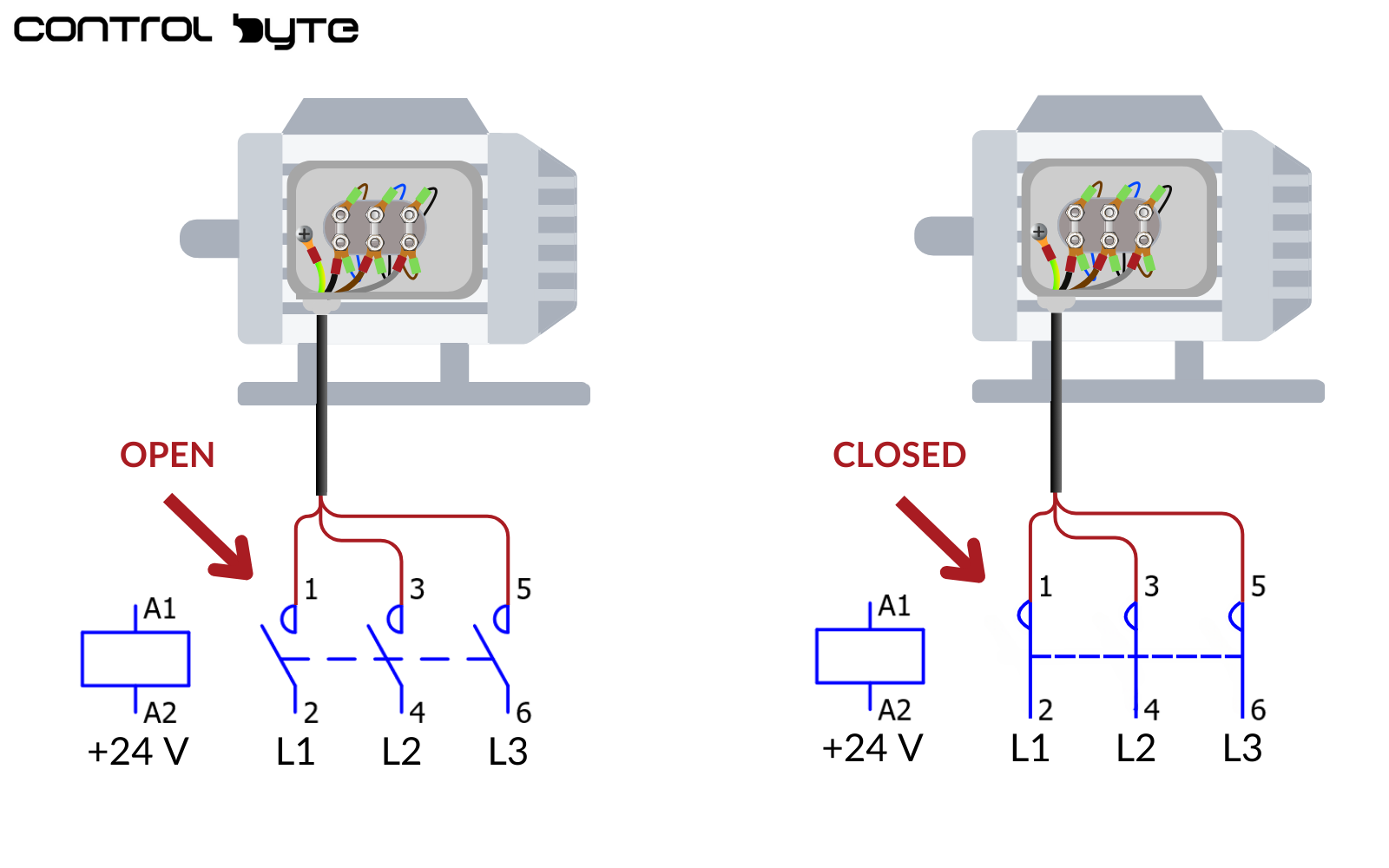
In the diagram below, there’s a button for turning the lamp on and off, but there isn’t one for the contactor. This raises the question: “How can the contactor be energized without a push button?”
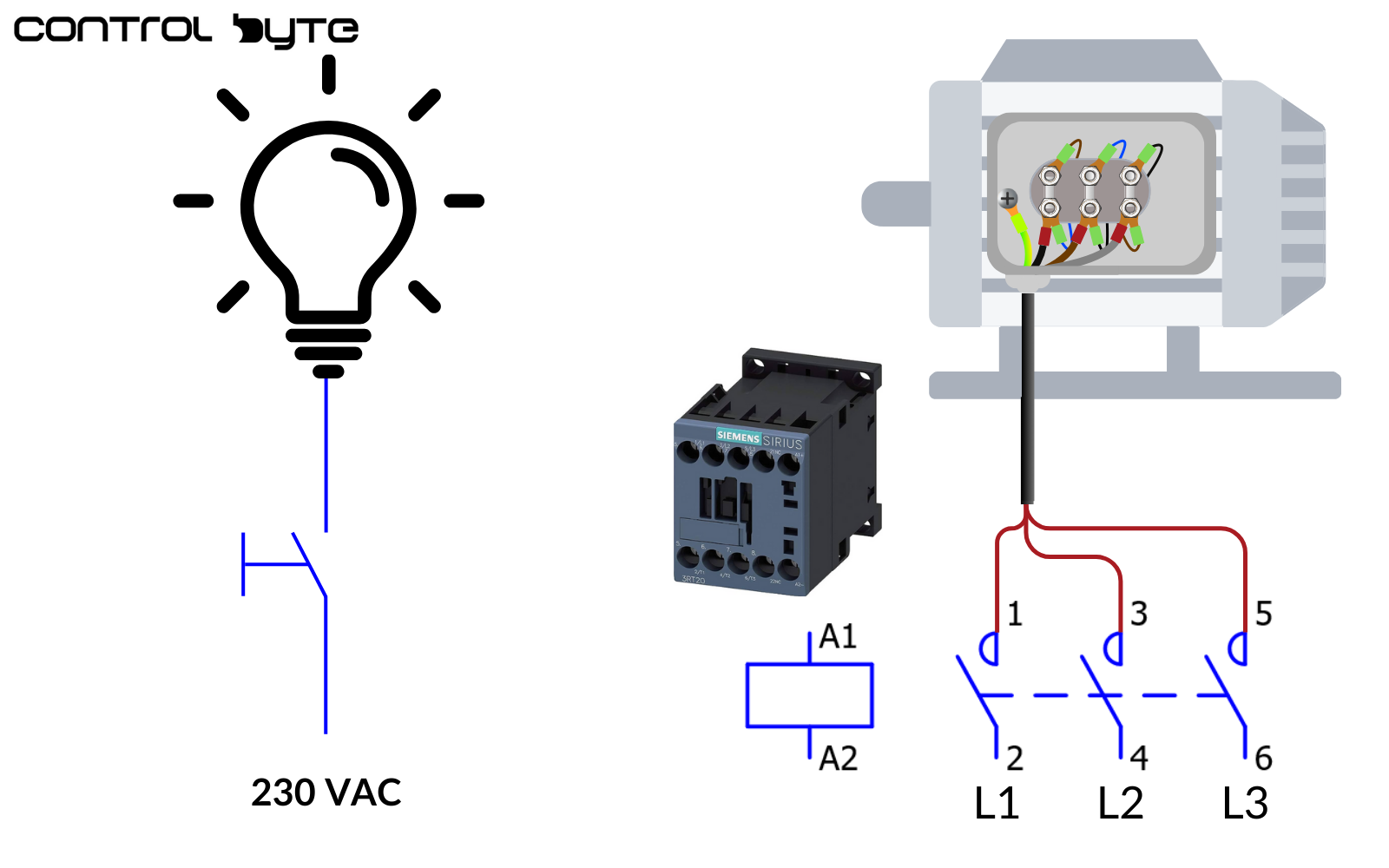
Using Star-Delta Starter Automation in PLC to Control 3 Phase Motor Start-Up and Reduce Current Draw
This can be achieved by connecting the contactor’s coil to a PLC output or another type of controller.
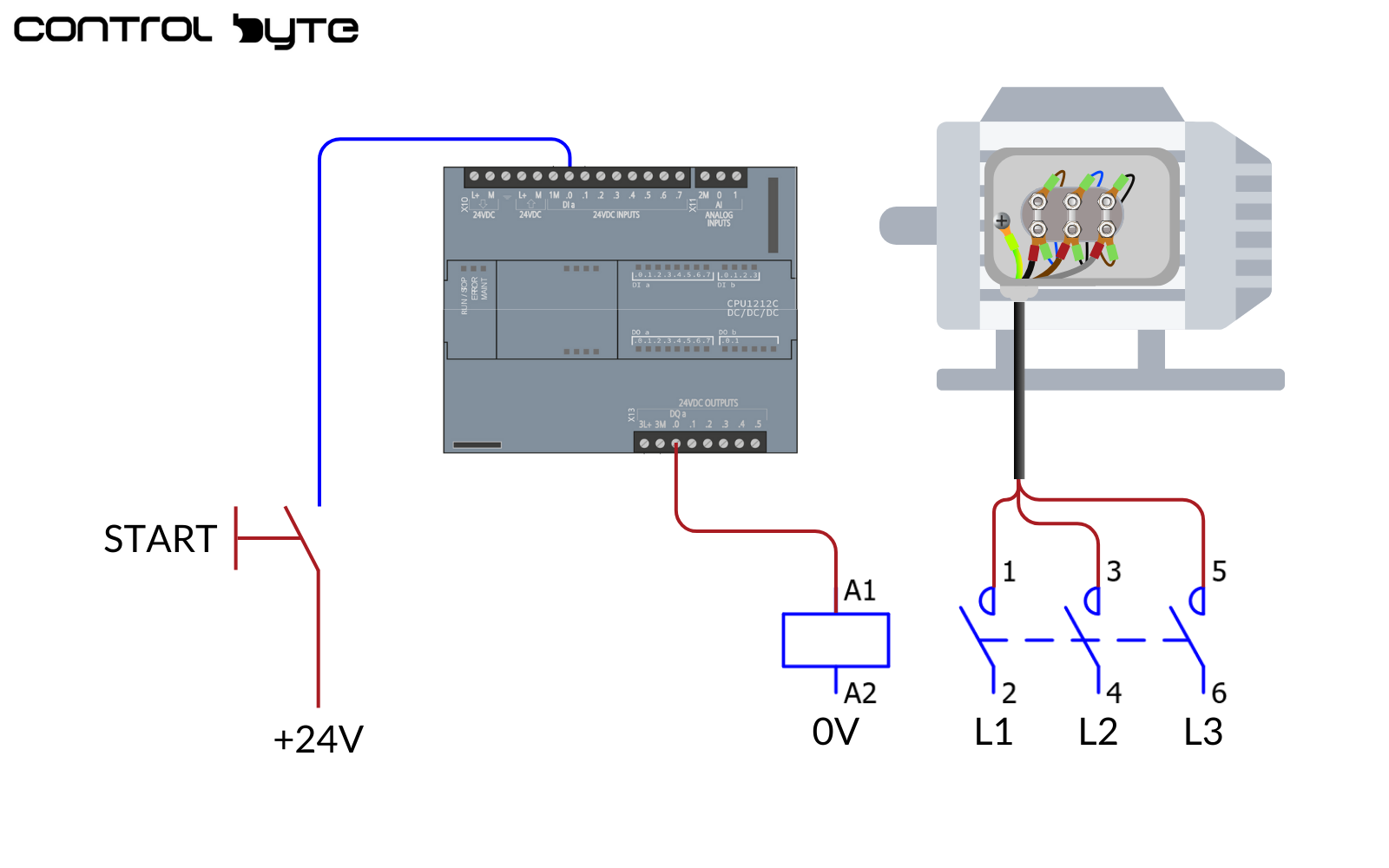
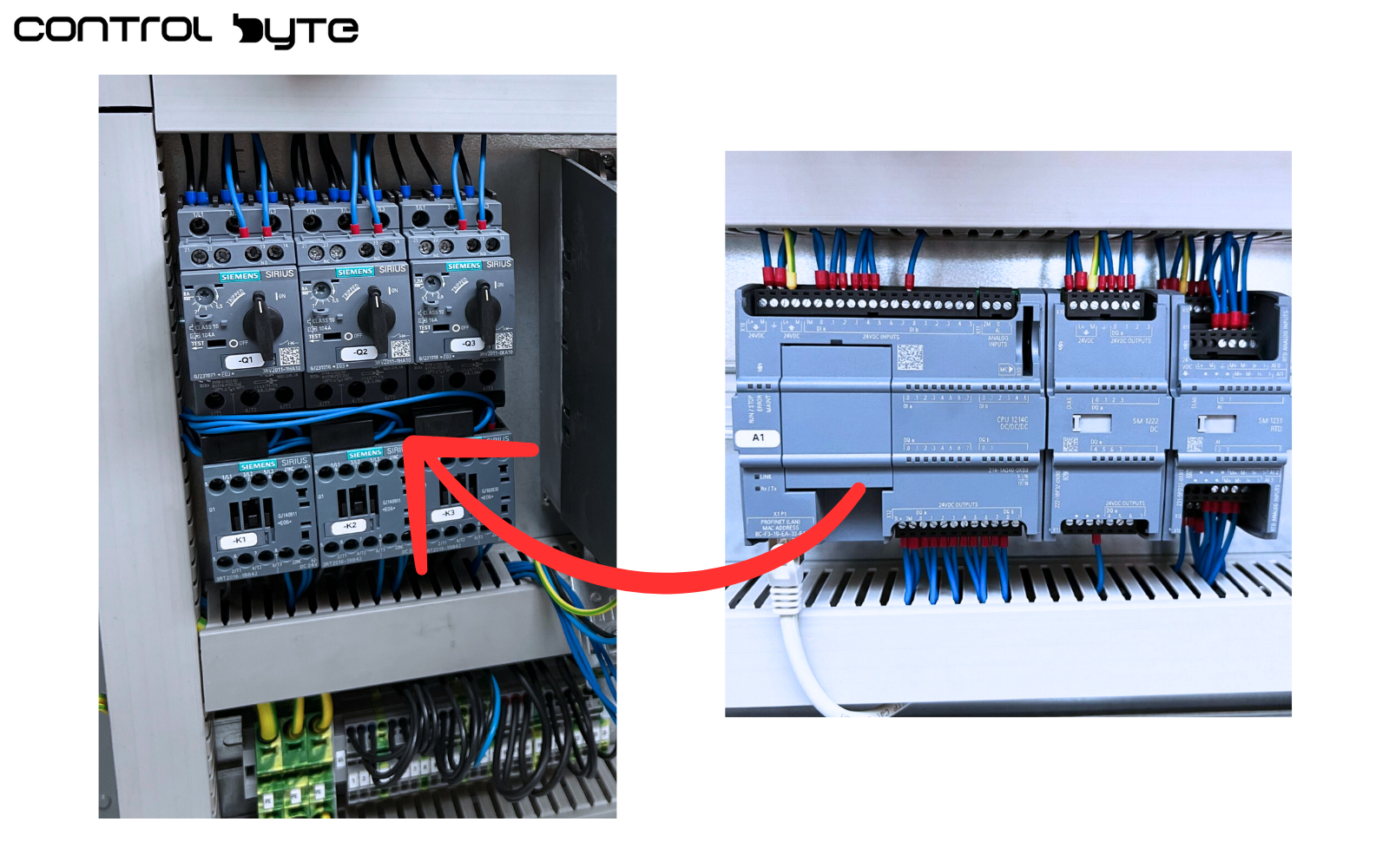
Here’s how to set it up: connect a simple switch to the PLC input. Then, using TIA Portal, write a basic code to energize the contactor’s coil whenever the start switch is pressed.
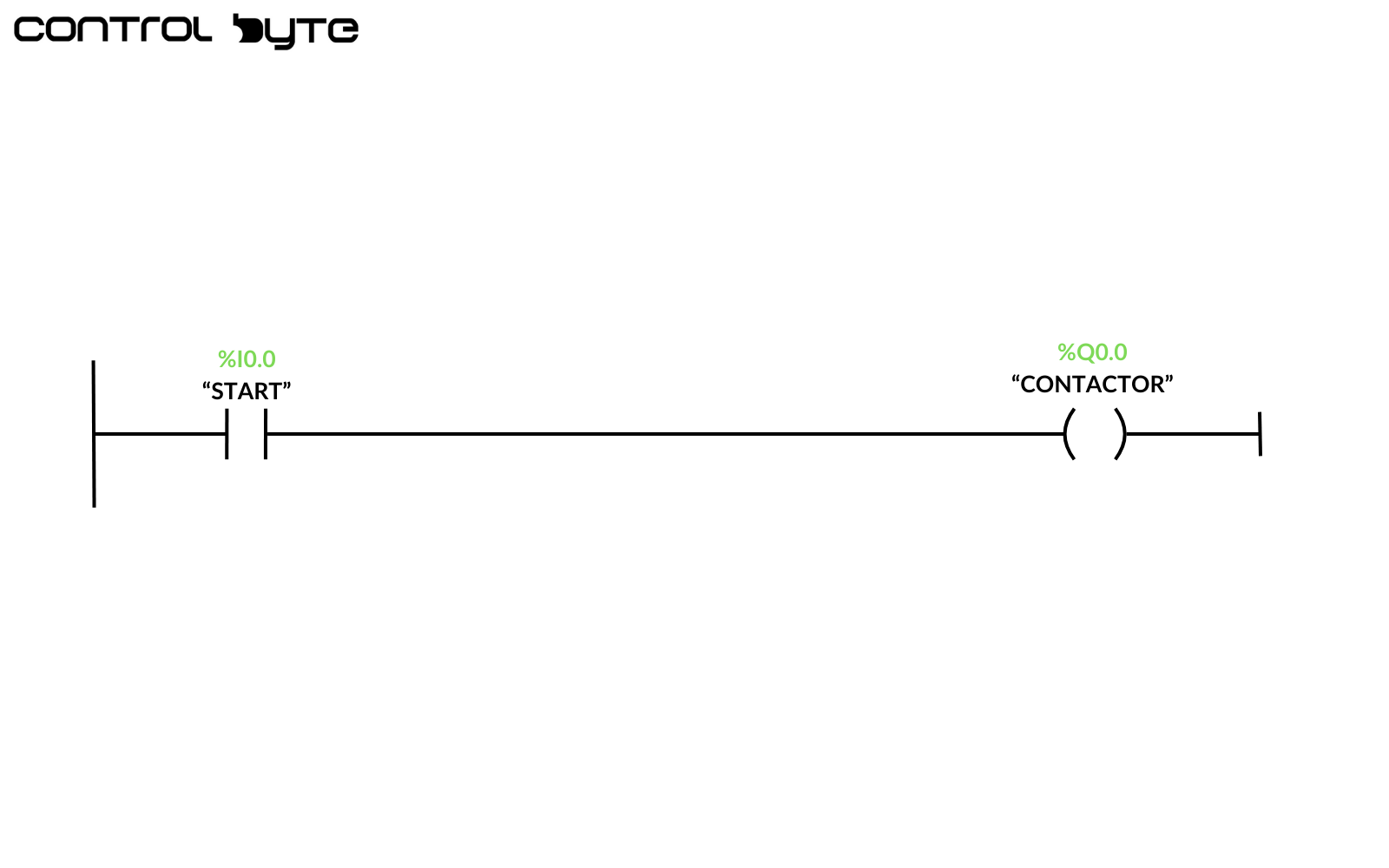
Once the program is written, it needs to be downloaded to the PLC. This allows the PLC to interpret the instructions for managing the input and output, effectively enabling it to perform the desired operation.
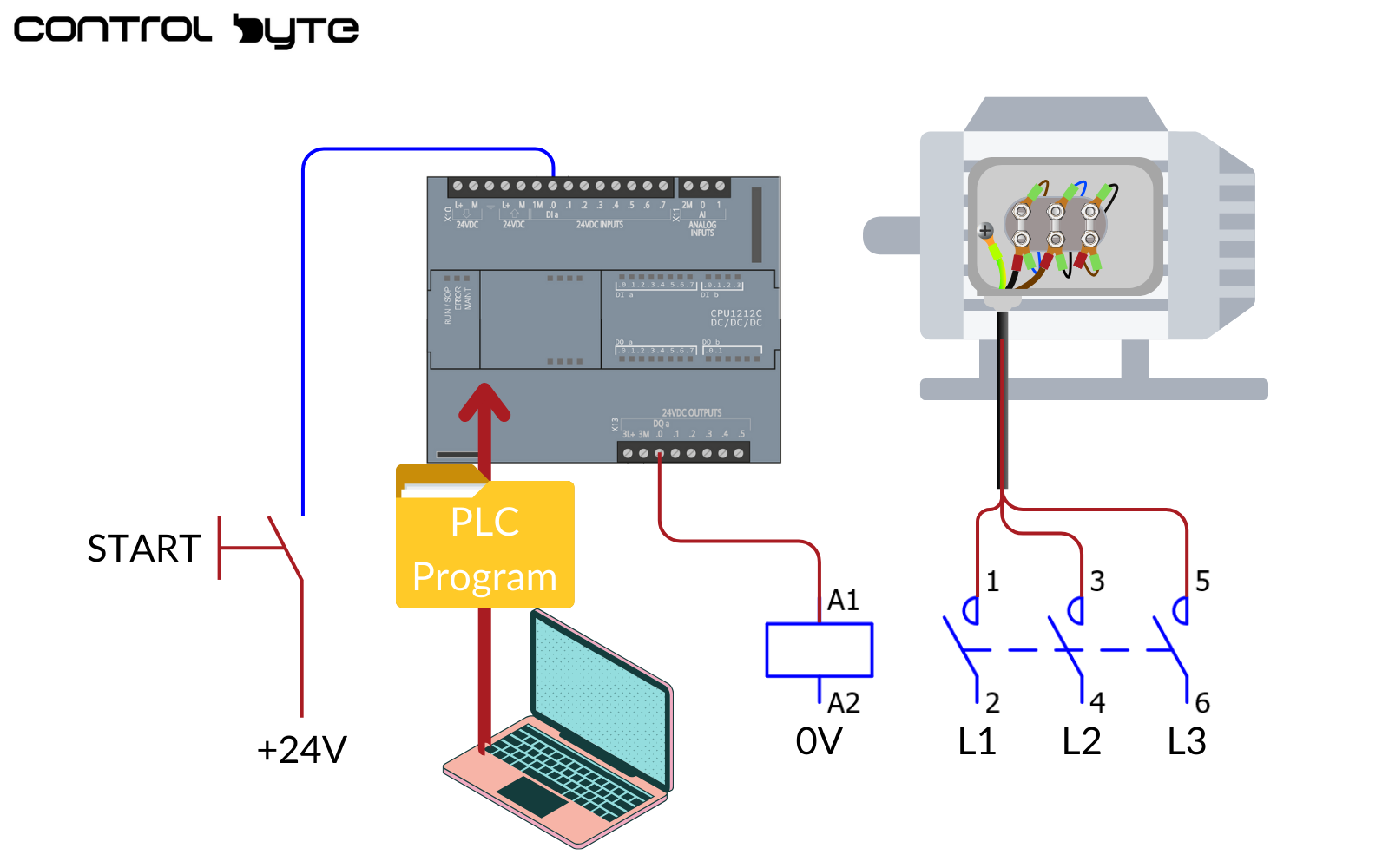
Why Star-Delta Starters Are Essential for 3-Phase Motor Protection and Reduced Voltage Starting
When you start a large electric motor, the initial inflow current can potentially damage both your equipment and electrical system. One effective way to prevent this is by using a star-delta starter.
IIn this post, we’ll explore how to use a star-delta starter to reduce a motor’s surge current effectively.
Let’s begin by examining the motor winding schematic. The upper ends of the windings are labeled U1, V1, and W1, while the lower ends are marked U2, V2, and W2. To start the motor, a three phase power source is connected to the upper ends—U1, V1, and W1.
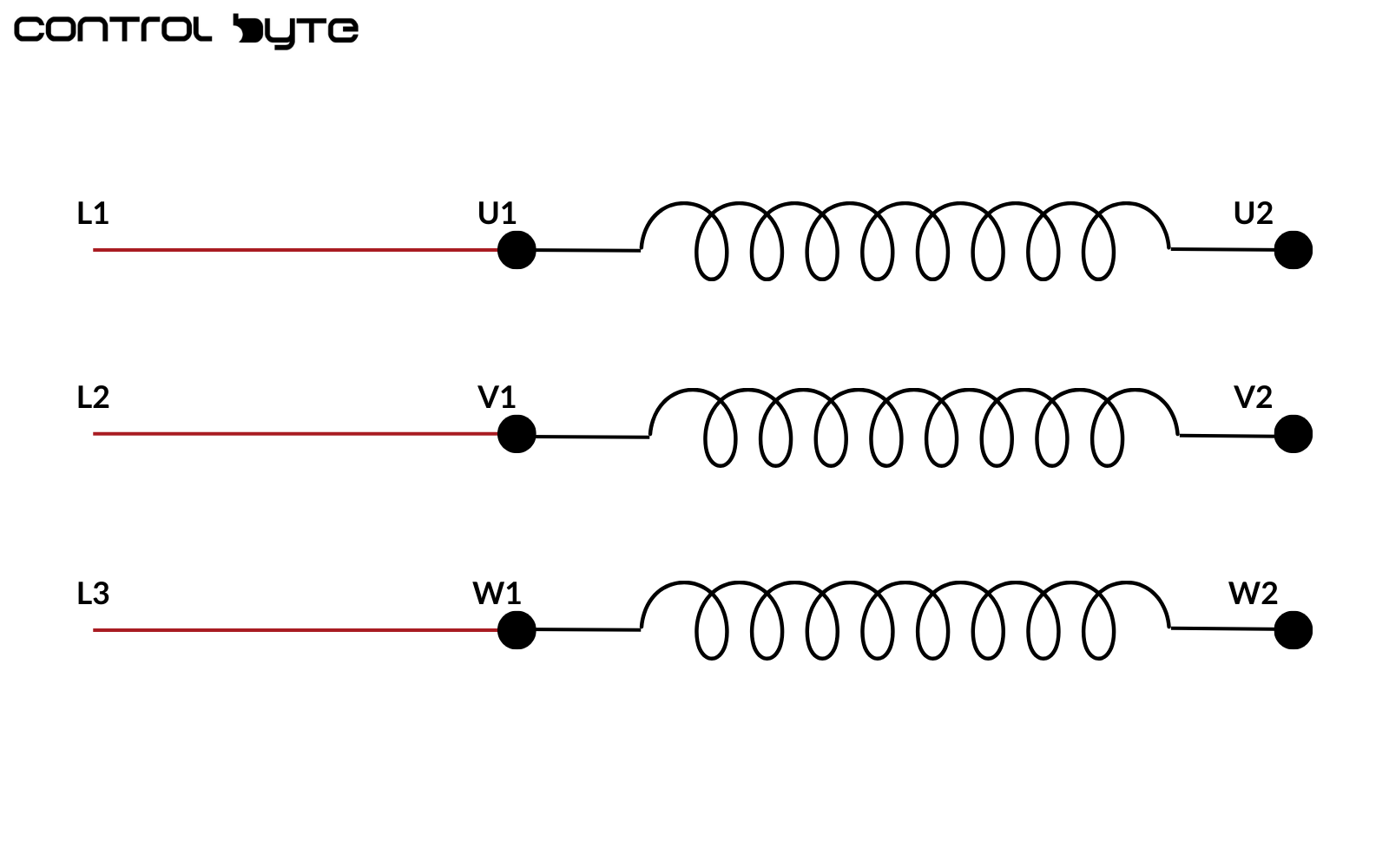
How to Connect 3-Phase Motor Windings in Star-Delta Configurations: Wiring and Control Principles
or a star connection, you simply connect the lower ends (U2, V2, and W2) together. In a delta connection, U1 connects to W2, V1 to U2, and W1 to V1
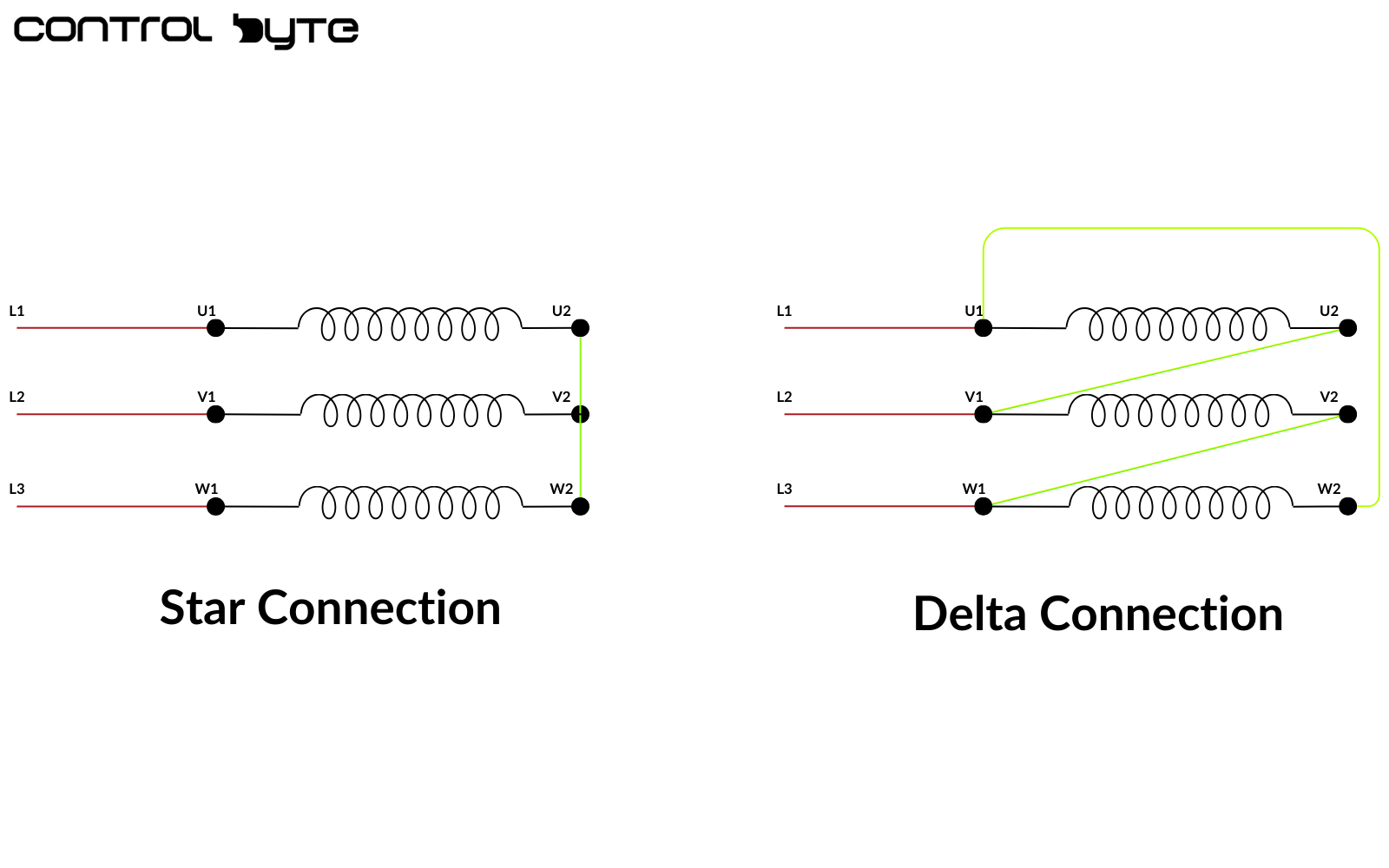
Connecting the windings in a star configuration reduces the motor’s starting current to one-third of its normal value. The concept behind a star-delta-starter is to start the motor in a star connection for a few seconds, reducing the surge current, and then switch to a delta connection once the motor has reached adequate speed.
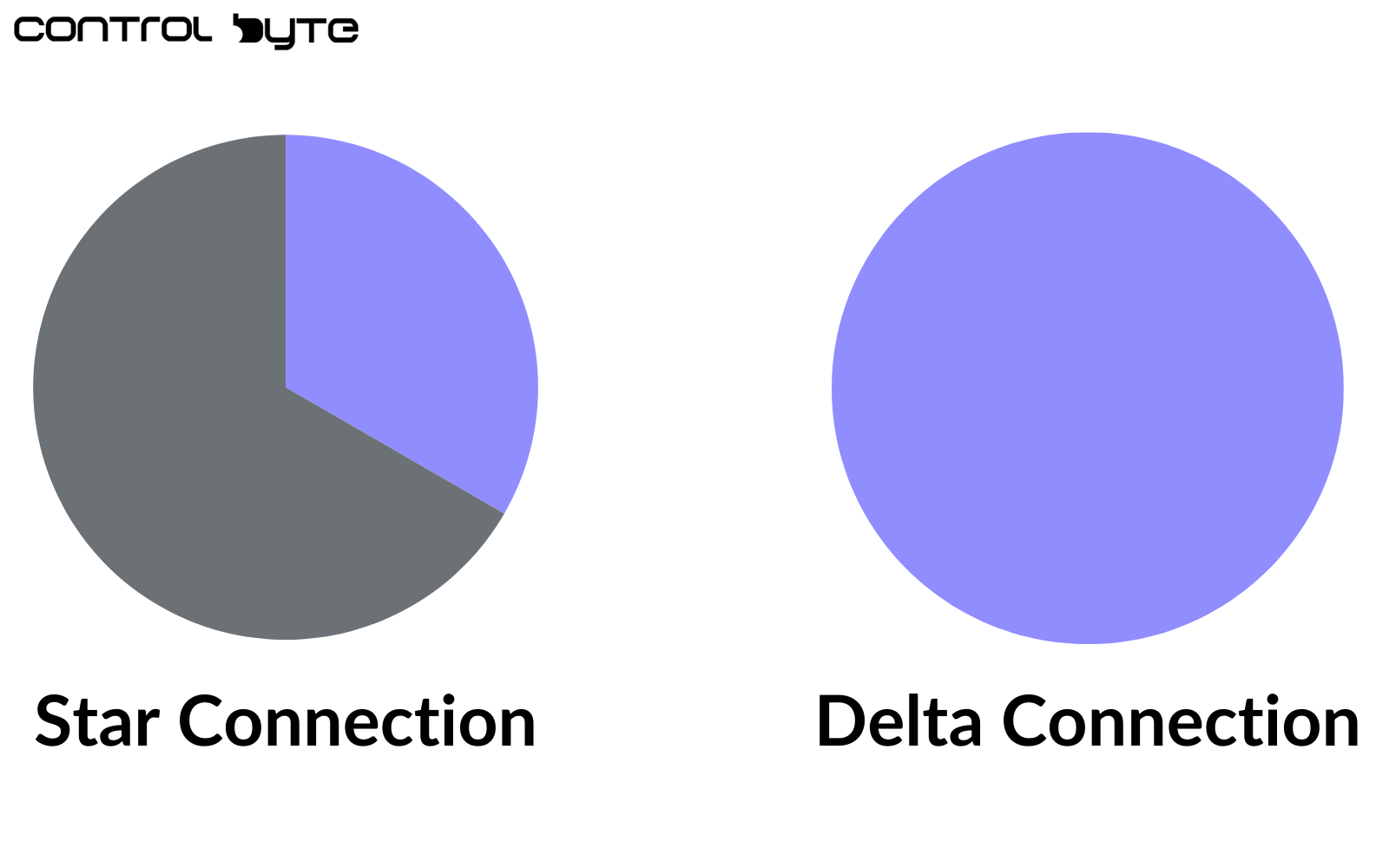
What Motor Start-Up Teaches Us: Handling High Energy and Current in Star-Delta Starting
An interesting point about this starting process is that the initial phase of motor start up, which draws more current, mirrors other areas of life: the beginning of any new endeavor often requires extra energy and focus. Isn’t it fascinating how this concept appears in different contexts?
How to Access Motor Terminals for Star and Delta Connections
Now that we understand how switching winding connections reduces start up current, the next question is: how do you access these winding terminals to connect power and switch between star and delta? Every three phase motor includes a connection board, giving access to all six winding ends..
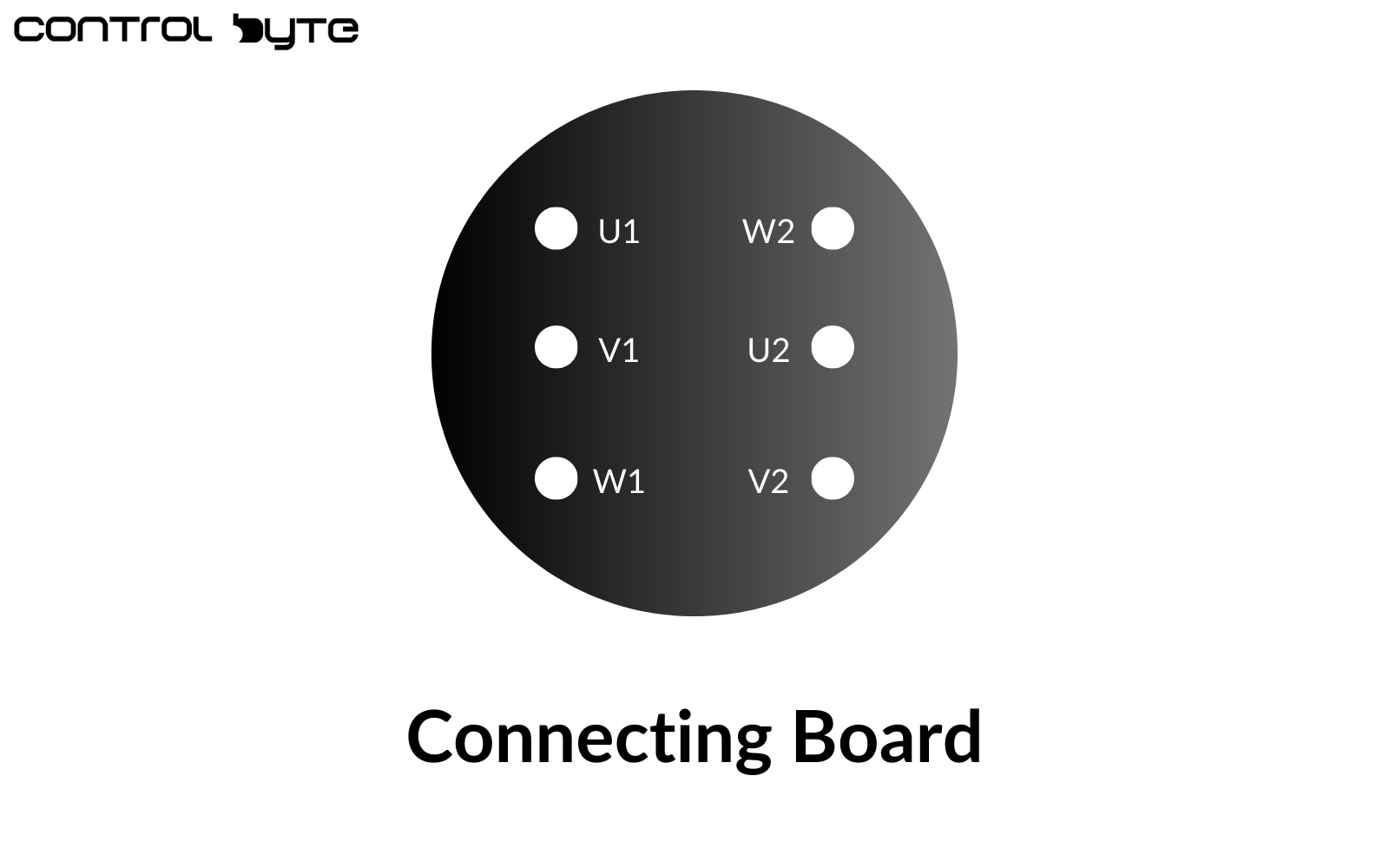
How to Access Motor Windings for Control Circuit Wiring and Star-Delta Starter Setup
Every electric motor contains copper windings that begin rotating once they’re connected to a power source.
To simplify, we represent these windings using three symbols: U1, V1, and W1 for the upper ends, and U2, V2, and W2 for the lower ends. In part 4 of the Star-Delta-Starter PLC Program and Wiring guide, we’ll explore how to access these winding ends in real-world motors.