“Welcome to the world of automation, young one… here, every detail matters” – this is a phrase I heard at the beginning of my journey with automation and PLC controllers.
It quickly became my motto!
Working with industrial automation requires precision, and every, even the smallest mistake, can have huge consequences.
That’s why understanding the operation of PLC controllers, such as the Siemens S7-1200, is crucial.
In this article, I will introduce you to the basics of the Siemens S7-1200 controller. I will discuss its construction, functions, and capabilities so that you can use it effectively in your projects.
Whether you are just starting your journey with automation or are looking for additional knowledge, this guide will help you take your first steps in the world of industrial automation solutions, where every detail matters!
Let’s get started!

What is the Siemens Simatic S7-1200 PLC?
It is a series of PLC controllers produced by the giant Siemens. Like other controllers, they are used in various industries, from oil refinery plants, through production lines, conveyor systems, to building automation systems.
Different CPU units with 24V DC power supply and their differences
The S7-1200 series is divided into many models with different parameters and applications. Below we present some of the models and their parameters:

They mainly differ in:
- Size of the enclosure
- Memory
- Number of inputs/outputs
- Expandability
- Number of HSC (High-Speed Counter) inputs
- Number of HSO (High-Speed Output) outputs


Digital and Analog Input/Output Expansion Module
Each CPU unit can be expanded with extension modules, of which there are 3 types – as shown in the image above. It is important to match the size of the controller to the location where it will be used, as even individual CPU units vary in size.

- Power Supply Dedicated for the S7-1200 PLC Controller
- A network switch in case there are not enough Ethernet ports.
- A communication module, such as IO-Link, RS422/485, Profibus, or CAN.
- The CPU, also known as the Siemens S7-1200 PLC unit.
- Technological modules, such as a weighing module or energy measurement module.
- IO modules, or otherwise, extensions for digital and analog input/output.
- Expansion cards, for example, adding several fast inputs and outputs.
For example, below – the S7-1200 controller expanded with the IO-Link technology module SM1278, used for communication with the inverter.

Remember, when choosing the Siemens S7-1200 PLC controller, you need to know that the number of modules you can connect to the CPU depends on the version of the controller you have – I will explain this further in the article.
External construction of the Siemens S7-1200 PLC CPU
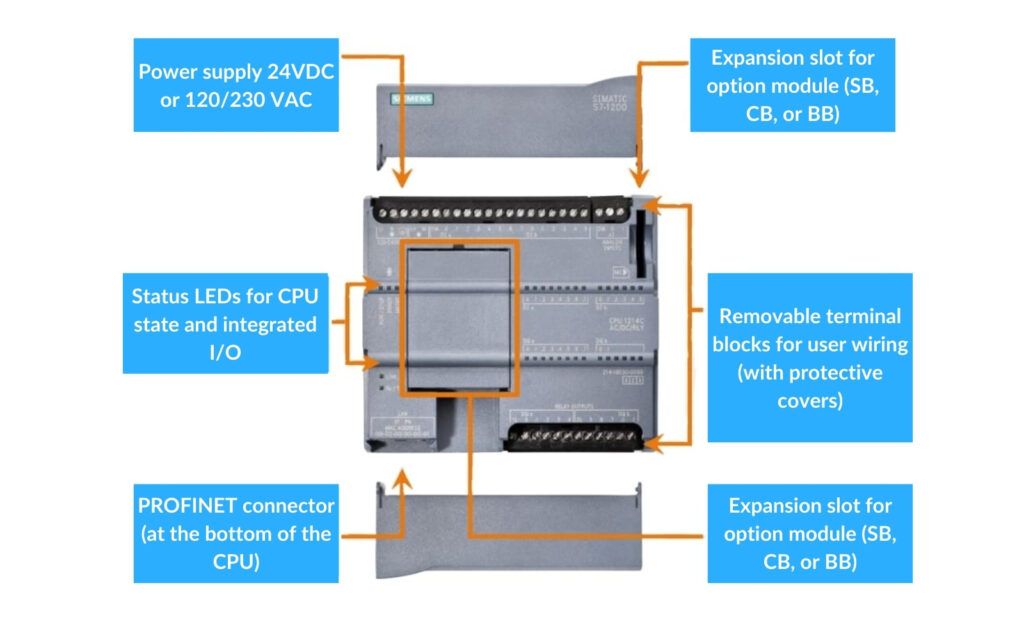
Key elements of the Siemens S7-1200 PLC controller:
- Terminal blocks
- Status LEDs for CPU and inputs/outputs
- PROFINET connector
- Slot for expansion cards
- Slot for memory card

Internal construction of the Siemens S7-1200 PLC CPU unit
Below, I’m posting a few pictures for electronics enthusiasts who want to get into automation. See what the S7-1200 controller looks like from the inside!


The Siemens S7-1200 PLC controller has a three-layer, stacked construction, with each board serving a specific role. Below is the corrected description of each layer:
Power board (bottom layer): This board contains components responsible for the power supply system of the controller. It includes all the necessary components for voltage stabilization and provides power to the upper layers. While this board does not have a direct power connection, the key components responsible for processing and delivering energy to the other parts of the controller are located here.
Middle board (expansion module): This is where the power connection is located, to which an external power source is connected. In addition to the power connection, this layer also handles the input and output connections, allowing the connection of peripheral devices such as sensors, actuators, and other elements of the automation system. Relays and optoisolators are also located on this board, protecting the signals.
CPU board (top layer): This is the most important board, containing the main processor (CPU), which is responsible for executing the control program and managing the entire operation of the device. This board also contains an Ethernet connection, enabling communication with other devices in the industrial network. The processor communicates with the other layers, controlling the flow of data and signals.



Versions of the Siemens S7-1200 PLC CPU
Below you will find 19 versions of the S7-1200 controller.
How to decode the designation, e.g., AC/DC/RLY?
The designation AC/DC/RLY at the beginning may seem unclear, but I will explain it. The controller I am talking about can be powered by a 230V AC power supply – hence the AC in the first position. DC in the second position indicates the type of digital inputs – transistor-based 24V DC, and RLY at the end means that your controller is equipped with relay outputs.
Meanwhile, the versions of the controllers surrounded by yellow rectangles indicate that they come with a built-in safety module, meaning that we do not need additional safety controllers or relays.
This is how Siemens designates its controller models.

Size of individual models of the S7-1200 PLC controller
The different versions also vary in size. The exact dimensions are provided in the graphic below.

Parameters of the Siemens S7-1200 PLC controllers
The controllers differ not only in size and power supply type for the CPU and inputs/outputs, but also in many other parameters, such as the number of inputs/outputs, memory, and expandability.
CPU | CPU 1211C | CPU 1212C | CPU 1214C | CPU 1215C | CPU 1217C | CPU 1212FC | CPU 1214FC | CPU 1215FC |
---|---|---|---|---|---|---|---|---|
Integrated PROFINET Ports | 1 | 1 | 1 | 2 | 2 | 1 | 1 | 1 1 |
Working Memory / Internal Memory | 50 KB / 1 MB | 75 KB / 2 MB | 100 KB / 4 MB | 125 KB / 4 MB | 150 KB / 4 MB | 100 KB / 2 MB | 125 KB / 4 MB | 150 KB / 4 MB |
Integrated Digital I/O | 6 DI 4 DO | 8 DI 6 DO | 14 DI 10 DO | 14 DI 10 DO | 10 DI 6 DO 4 DI 1) 4 DO 1) | 8 DI 6 DO | 14 DI 10 DO | 14 DI 10 DO |
Analog Signals | 2 AI | 2 AI | 2 AI | 2 AI 2 AQ | 2 AI 2 AQ | 2 AI | 2 AI | 2 A1 2 AQ |
Integrated HSC | 6 @100kHz | 6 @100kHz | 6 @100kHz | 6 @100kHz | 3 @100kHz 3 @1MHz | 6 @100kHz | 6 @100kHz | 6 @100kHz |
Pulse Outputs | 4 | 4 | 4 | 4 | 4 | 4 | 4 | 4 |
Expansion Capabilities | 3 – CM 1 – SB | 3 – CM 1 – SB 2 – SM | 3 – CM 1 – SB 8 – SM | 3 – CM 1 – SB 8 – SM | 3 – CM 1 – SB 8 – SM | 3 – CM 1 – SB 2 – SM | 3 – CM 1 – SB 8 – SM | 3 – CM 1 – SB 8 – SM |
Maximum Number of Modules for the Siemens S7-1200 PLC
As I explained earlier, attention should be paid to the expansion capabilities of a particular version of the CPU controller. The higher the CPU model, the more modules we can connect to it – see the graphic below.

Available Expansion Modules on the Market
In Siemens’ offering, you will find almost every module you can think of, well, except for WiFi 🙂 Below, I will present the expansion options for the S7-1200 CPU.
Binary Input and Output Modules and Technological Modules for S7-1200

Which communication module for S7-1200?

Communication of the Siemens S7-1200 Controller
The Siemens PLC controller offers a wide range of communication protocols, allowing us to exchange data with other automation devices. Below is a list of available protocols:
- PROFINET
- PROFIBUS Master / Slave
- OPC UA Server
- AS-i Master
- BACNet Client/Server*
- CANopen Master*
- TCP/IP Protocols (Modbus TCP, MQTT, HTTP, etc.)
- IO-Link Master
- GSM/GPRS/LTE
- DNP3, IEC 60870-5-104
- RFID
- PtP (RS-485, RS-422 & RS232)
- Modbus RTU
- USS Protocol (Universal Serial Interface Protocol)

Integrated PID Controllers in S7-1200 – CPU 1212c
The S7-1200 controller features advanced integrated PID controllers that enable process control automation. With the autotuning function, the system automatically adjusts the PID loop parameters, simplifying tuning and control optimization.
Users have access to easy-to-configure screens, allowing for quick implementation and real-time monitoring of the process, which is particularly useful during system startup.

Integrated Motion Control in S7-1200
The S7-1200 controller also supports motion control, including speed and position control. With integrated support for stepper motors and servo drives, the S7-1200 can manage various drive systems using PTO (Pulse-Train Output) or communication protocols such as PROFIdrive (PROFINET/PROFIBUS).

Which license to choose for TIA Portal?
The slide shows that Step 7 (TIA Portal) Basic supports S7-1200 and S7-1200 F controllers and provides support for the PLCSIM simulator and Basic HMI panels. This is the basic version of the software, mainly targeted at these devices.

Other controllers, such as S7-300 F, S7-400 F, S7-1500 F, as well as Open Controller and Software Controller, are supported exclusively by Step 7 Professional, which also offers Step 7 Safety Advanced (optional).
Applications: Hydraulic press on Siemens S7-1200 PLC.

At the machine, such as a hydraulic press, we will need to program the following components:
- Pressure Sensors:
Used to monitor and regulate pressure in the hydraulic system of the press. They ensure consistent control over the pressing force, which is crucial for the quality of the performed operations. - Position Sensors:
Allow precise determination of the position of movable parts of the press, such as the piston. These are essential for accurate control of the pressing process and ensuring repeatability of operations. - Digital Manometers:
Serve for precise reading of pressure in the hydraulic system. They can be used for monitoring and recording pressure data in real time, enabling analysis and optimization of the process. - HMI Interfaces:
Touchscreens or operator panels that allow the user to interact with the machine, set working parameters, visualize processes, and perform diagnostics. - Safety Systems:
Including light barriers, safety mats, and emergency buttons, which protect the operator from injuries. These systems are designed to automatically stop the machine’s operation when a dangerous situation is detected. - Encoders:
Devices measuring rotation or position, which can be used for precise control of the piston’s movement or other movable parts of the press.
Applications: HVAC ventilation system on Siemens S7-1200 PLC
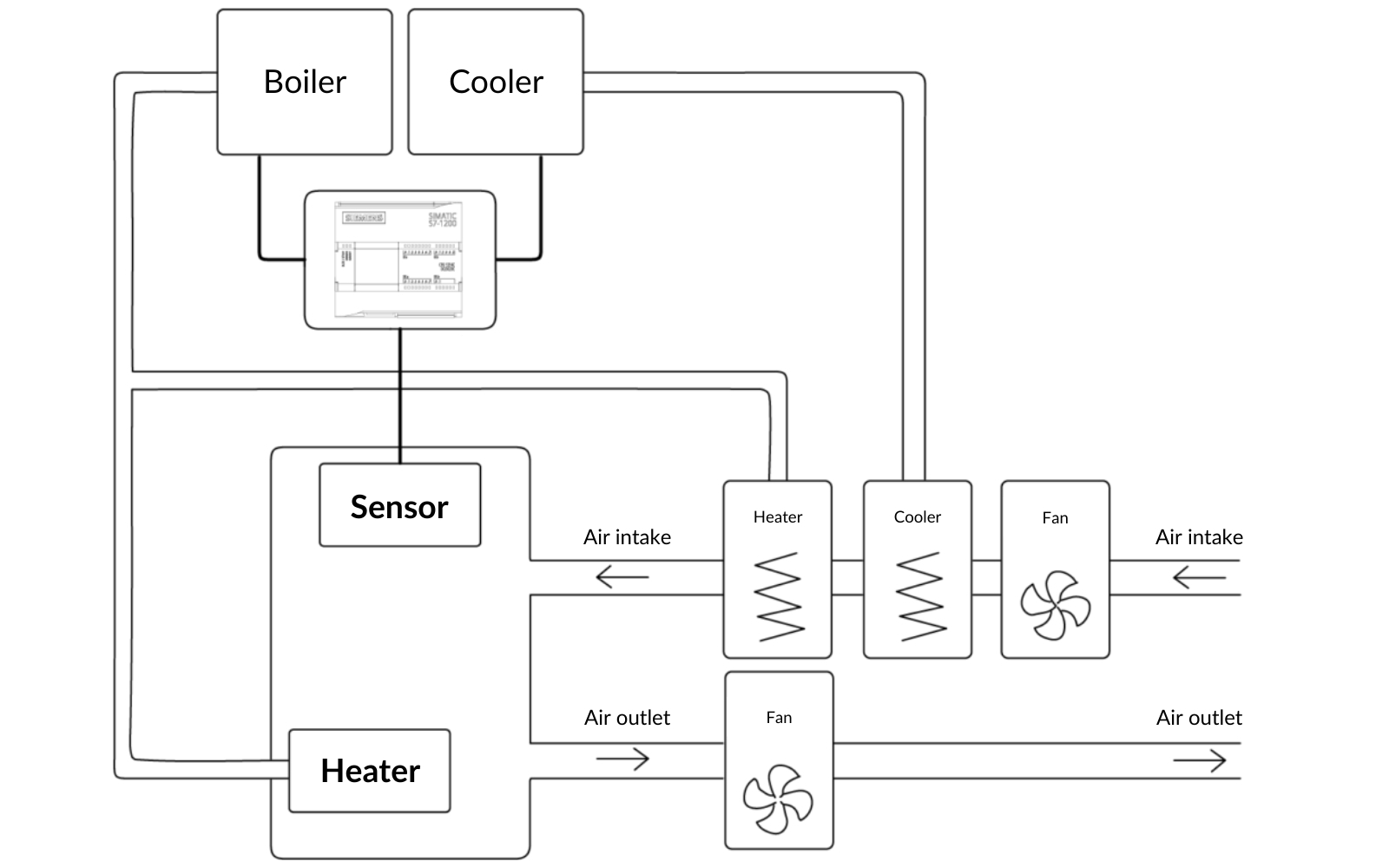
In HVAC systems using Siemens S7-1200, you can control the following components:
- Thermostats:
Enable temperature regulation in rooms directly from the controller, based on a programmed schedule or user behaviors. - Temperature and Humidity Sensors:
Monitor room conditions and are critical for automatic HVAC adjustments to maintain desired climate conditions. - Controlled Dampers and Valves:
Allow precise control of the flow of hot or cold air and water in heating and cooling systems, ensuring proper temperature and air distribution across different building zones. - Motion Sensors:
Can be integrated with HVAC systems to automatically adjust climate settings depending on the presence or absence of people in a room. - Smart Windows:
Utilizing dimming technology or special coatings, they can automatically adjust the amount of sunlight entering a room, impacting its heating and reducing the need for air conditioning. - Integrated Lighting Systems:
Can automatically adjust lighting levels based on available natural light, which also affects room temperature. - Programmable Fans and Pumps:
Equipped with variable speed drives (e.g., inverters) to adjust their operation according to real-time demand, reducing energy consumption.
Applications: Drives controlled by Siemens S7-1200 PLC
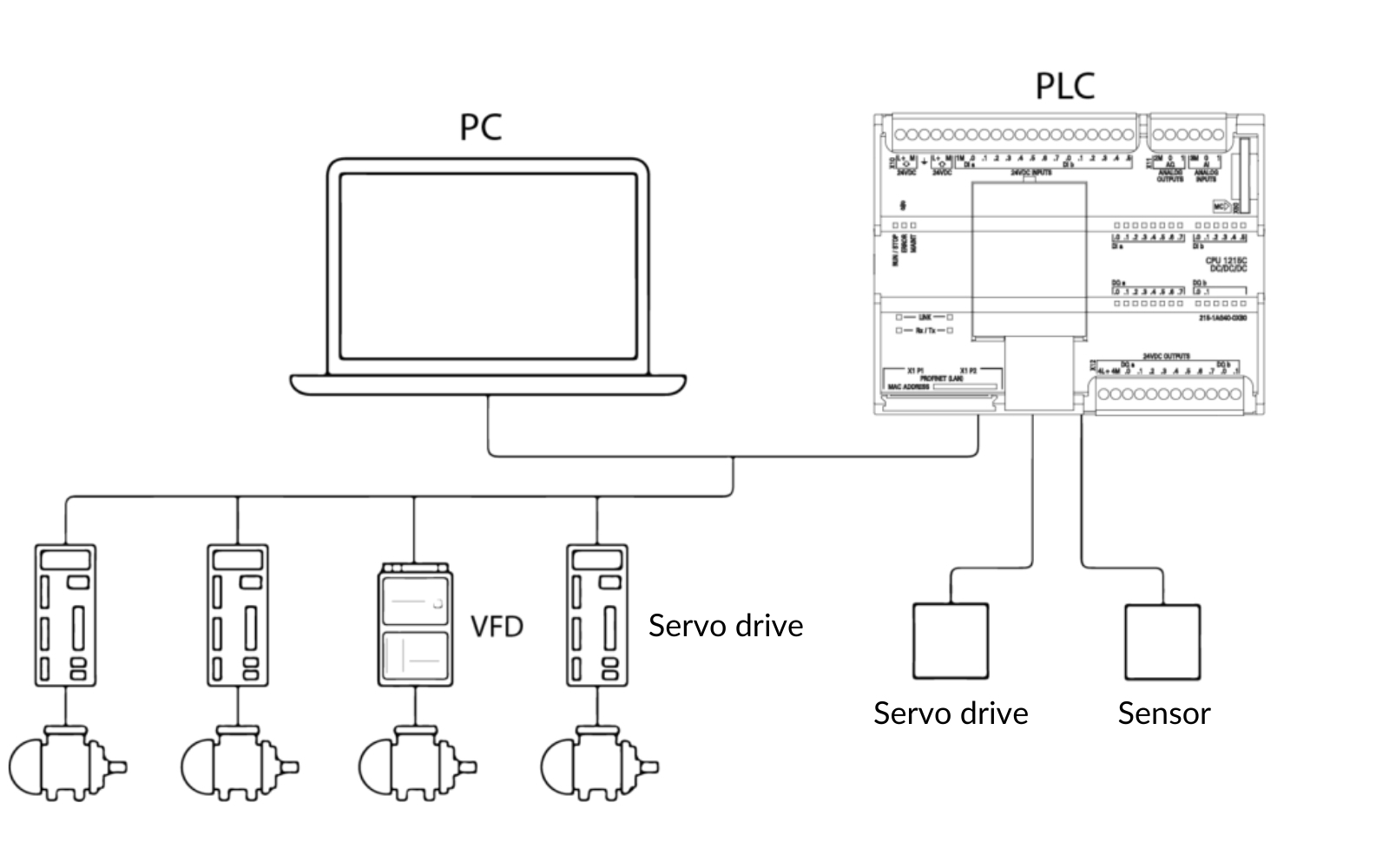
- AC Electric Drives:The S7-1200 can control AC drives through analog or digital signals, using appropriate output modules. Communication protocols such as Modbus RTU can also be utilized to control drives via a serial interface.
- DC Electric Drives:Similar to AC drives, DC drives can be controlled through direct signals from the PLC or via digital communication.
- Servo Drives:The S7-1200 can control servo drives using analog control signals (for simple position or speed control) or advanced communication interfaces such as Profinet, provided the drives have the required communication modules.
- Stepper Drives:The controller can operate stepper drives using digital output signals for precise motion control. Step sequences can be programmed directly within the controller logic.
- Motors with Frequency Converters (Inverters):The S7-1200 can control inverters via analog signals (for speed regulation) or digital communication, such as Modbus RTU or Profinet, enabling more complex control, including vector control.
Applications: Industrial furnace on Siemens S7-1200 PLC.
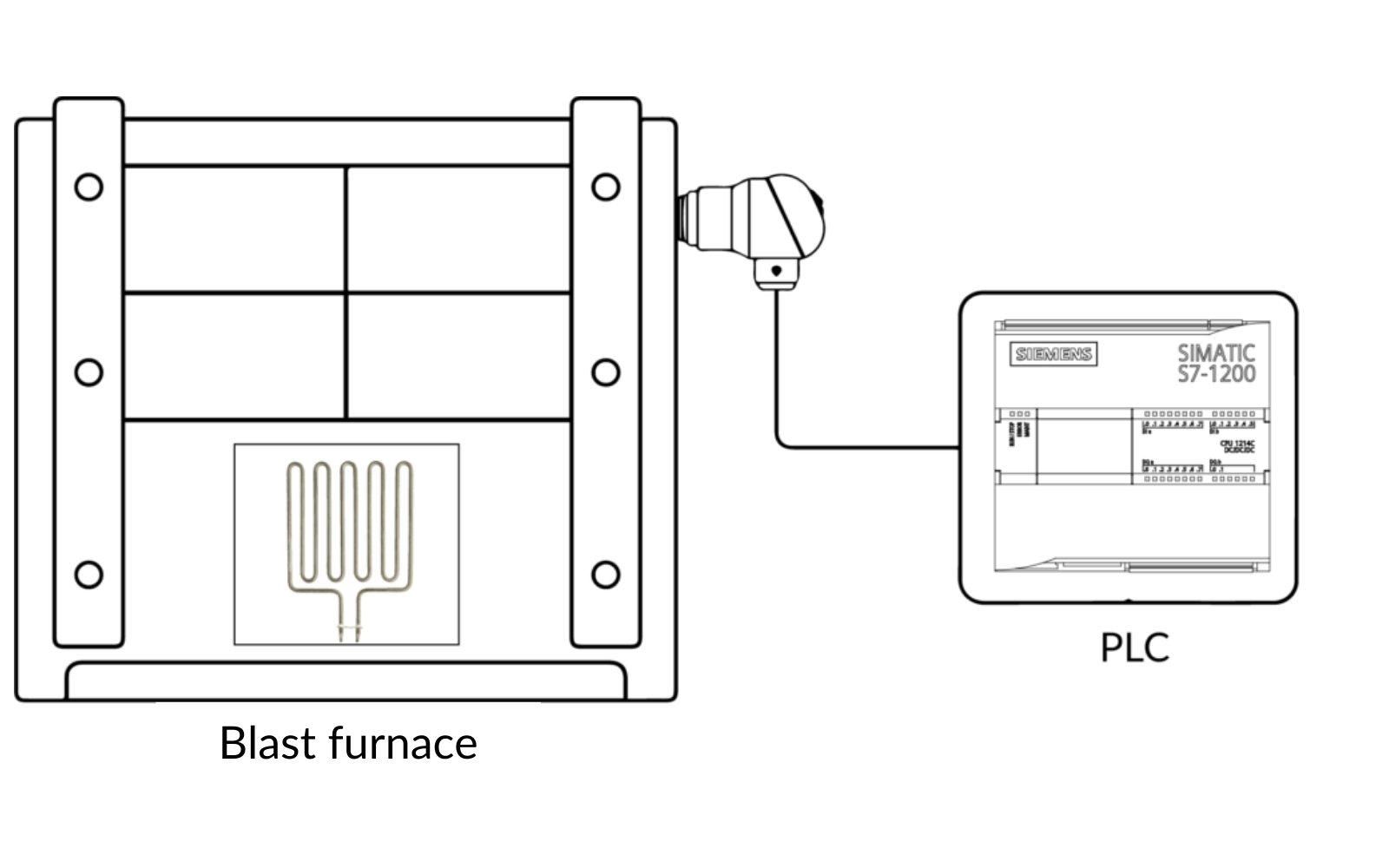
Devices and Functions for Controlling an Industrial Furnace:
- Temperature Sensors:
Commonly used types include thermocouples and RTD (Resistance Temperature Detectors), which measure temperature at various points within the furnace. Data from these sensors is essential for regulating the heating process. - PID Controllers (Proportional-Integral-Derivative):
These are software functions within the PLC that enable precise temperature control in the furnace. They operate based on readings from temperature sensors, automatically adjusting the heating power to maintain the desired temperature. - Control of Heating Elements:
Depending on the furnace type and heating elements (e.g., resistors, gas burners, induction elements), the PLC can manage their operation through relays, contactors, SSR (Solid State Relay) power controllers, or analog output modules for power regulation. - Ventilation and Blower Systems:
Controlling airflow within the furnace is important for maintaining an even temperature distribution and for processes requiring a specific atmosphere inside the furnace chamber. The PLC can manage the operation of fans and damper valves. - Timed and Sequential Programs:
The PLC allows for programming complex furnace operation sequences, including heating, temperature maintenance, and cooling phases, which are critical in processes like heat treatment of metals or ceramic firing. - HMI Interfaces:
Enable operators to monitor furnace status, input process settings, start firing programs, and quickly diagnose any issues. - Alarm and Safety Systems:
Designed to monitor and respond to abnormal furnace operating conditions, such as exceeding maximum temperature, heating element failures, or ventilation issues. The PLC can automatically shut down the furnace upon detecting a fault, minimizing risks. - Communication Modules:
Allow integration of the PLC with other systems in the facility, enabling remote monitoring, diagnostics, and process control, as well as data collection for process analysis and optimization.
Applications: Pumping station on Siemens S7-1200 PLC.

Automating a water pumping system with a PLC like Siemens S7-1200 facilitates efficient pumping processes, monitoring, and energy optimization. Below are key components and functions utilized in such systems:
- Pumps:
Core components of the water pumping system. The PLC can control various types of pumps, such as submersible, centrifugal, and multistage pumps, depending on system requirements. - Inverters (Variable Frequency Drives – VFDs):
Enable variable motor speed control, allowing precise adjustment of water flow to meet current system demands. PLC-controlled inverters optimize energy consumption and reduce mechanical wear on pumps. - Flow Sensors:
Measure the amount of water flowing through the system. Data from these sensors is used by the PLC to regulate pump operation, ensuring appropriate water flow. - Water Level Sensors:
Monitor water levels in tanks, wells, or reservoirs. The PLC can automatically start or stop pumps based on water levels, preventing overflow or dry running. - Valves:
The PLC can control system valves to regulate water flow, direct water to different sections, or isolate parts of the system for maintenance or emergencies. - Relays and Contactors:
Used for controlling high-voltage pump circuits, enabling the PLC to directly turn pumps on or off. - HMI Interfaces:
Allow operators to easily monitor and control the pumping system. HMIs display key information such as current flow rates, water levels, pump status, and alarms, and provide manual control options. - Alarm Systems:
The PLC can monitor system irregularities, such as pump dry running, high/low water pressure, or pump failures, generating alerts or automatically initiating corrective actions. - Programmable Operating Sequences:
The PLC enables the programming of automatic sequences, such as cyclic water pumping, automatic pump switching during failures, or controlling cleaning and disinfection processes in water treatment systems. - Thank you for reading! If you’re interested in learning more, explore our courses for in-depth training: Control Byte Courses.
Applications of PLC S7-1200 in Various Market Segments
OEM
- Conveyors
- Elevators
- Material Handling Machines
- Metal Processing
- Packaging
- Printing
- Textiles
- Mixers
- AGV (Automated Guided Vehicles)
Remote communication
- Simple Manipulators
- Stacking Machines
- Conveyors
- Dispensers
- Material Handling
- Packaging
- Printing
- Textiles
- Welding
Motion Control
- Cold Storage Control
- Energy Management
- Fire Protection
- HVAC
- Lighting Control
- Pump Control
- Access Security
- Transportation
- Irrigation
- Garage Door Control
- Car Washes
- Bowling Alleys
- Traffic Control
Infrastructure
- Oil/Gas Pumping Stations
- Petrochemical Gas Pumping Stations
- Electricity Distribution
Thank you for reading! If you’re interested in learning more, explore our courses for in-depth training: Control Byte Courses.